Газораспределительный механизм
- О газораспределительных механизмах карбюраторных двухтактных двигателей см. Двухтактный двигатель
В статье не хватает ссылок на источники (см. также рекомендации по поиску). |
Возможно, эта статья содержит оригинальное исследование. |
Стиль этой статьи неэнциклопедичен или нарушает нормы литературного русского языка. |
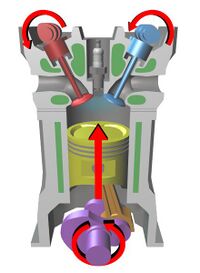
Газораспределительный механизм (ГРМ) — механизм, обеспечивающий впуск чистого воздуха и выпуск отработанных газов из цилиндров. Может иметь как фиксированные фазы газораспределения, так и регулируемые, в зависимости от частоты вращения коленвала и других факторов.
Чаще всего состоит из распределительного вала или нескольких валов привода распределительного вала, коромысел, пружин, клапанов, поршней и коленчатого вала. В некоторых конструкциях система распределения представлена вращающимися или качающимися распределительными гильзами или золотниками.
Система привода распределительного вала четырёхтактного двигателя в любом случае обеспечивает его вращение с угловой скоростью, равной 1/2 угловой скорости коленвала[1].
Характеристики ГРМ
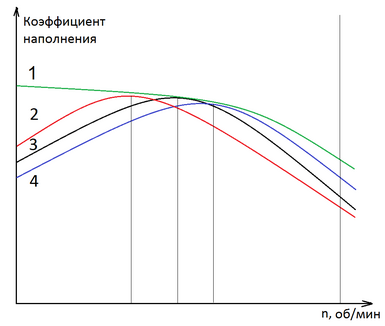
- Сопротивление впускного и выпускного трактов, ограничивающее быстроходность и снижающее наполнение на более высоких оборотах. Определяется пропускными сечениями клапанов и патрубков, шероховатостью каналов, их изгибом, настройкой (инерционный наддув). При росте сопротивления пики максимума наполнения сдвигаются в область меньшего числа оборотов, что ограничивает мощность ДВС[2].
- Настройки фаз газораспределения (углы опережения открытия впускных и выпускных клапанов/золотников, углы запаздывания закрытия). Эти настройки позволяют частично компенсировать сопротивление впускных и выпускных трактов, сместив максимум наполнения цилиндров от нулевой частоты вращения (при нулевых углах) до частоты, заданной конструктором. Обычно, максимум наполнения соответствует максимуму крутящего момента. На рисунке представлены кривые, соответствующие VVT (1), тихоходной настройке (2), настройке примерно на 0,5 максимальной частоты вращения (3), и скоростной настройке (4)[3].
- Возможность получения компактной камеры сгорания (минимальных размеров) и низкой температуры в районе догорания топливной смеси (искровые ДВС). Это позволяет иметь меньше всего газов в области гашения пламени (что снижает выбросы), и улучшить экономичность[4].
- Коэффициент остаточных газов, возможность турбулизации заряда; простота, дешевизна, надёжность, габариты и общая масса деталей.
Типология
Классификация механизмов газораспределения производится в зависимости от того, каким образом в них осуществляется управление впуском и выпуском. Обычно выделяют четыре типа механизмов управления впуском и выпуском:
- поршневые;
- золотниковые;
- клапанные;
- гильзовые.
С поршневым управлением газораспределения
Механизм газораспределения с поршневым управлением впуском и выпуском (он же — оконный газораспределительный механизм) применяется на двухтактных двигателях с кривошипно-камерной продувкой. В нём фазы газораспределения задаются за счёт осуществляемого непосредственно поршнем открытия и закрытия окон в стенке цилиндра.
Впускное окно обычно открывается при положении коленчатого вала, в котором поршень не доходит 40-60° до нижней мёртвой точки (по углу поворота коленвала), а закрывается спустя 40-60° после её прохождения, что даёт достаточно узкую фазу впуска — не более 130—140°. На высокофорсированных спортивных моторах открытие впускного окна может производиться за 65-70° до НМТ, что расширяет фазу впуска, но при этом работа двигателя на малых и средних оборотах становится неустойчивой, значительно увеличивается непроизводительный расход топлива из-за обратного выброса топливной смеси в атмосферу.
Выпускное окно открывается примерно за 80-85° до достижения поршнем нижней мёртвой точки, а закрывается спустя 80-85° после её прохождения, что даёт длительность фазы выпуска около 160—165°. Фаза продувки имеет длительность около 110—125°.
Симметричность фаз газораспределения при поршневом управлении впуском и выпуском обусловлена тем, что взаимное расположение поршня и окон в стенке цилиндра одинаково как при ходе вверх, так и при ходе вниз. Это является недостатком, поскольку для оптимальной работы двигателя как минимум фаза впуска должна быть асимметрична, что при чистом поршневом управлении газораспределением недостижимо. Для получения таких характеристик в малых двухтактных двигателях с кривошипно-камерной продувкой используются золотниковое газораспределение или лепестковый клапан на впуске (см. ниже).
В двухтактных двигателях большого объёма (тепловозные, морские, авиационные, танковые) либо на один цилиндр два поршня, движущихся навстречу друг другу, один из которых открывает впускные окна, а второй — выпускные (прямоточная продувка), либо через окна в стенке цилиндра производится только впуск, а выпуск осуществляется с помощью клапана в головке цилиндров (клапанно-щелевая продувка), при этом также достигается более оптимальная продувка.
В роторно-поршневых двигателях также как правило используется управление газораспределением поршнем (ротором), играющим в данном случае роль золотника[5].
С золотниковым управлением газораспределением
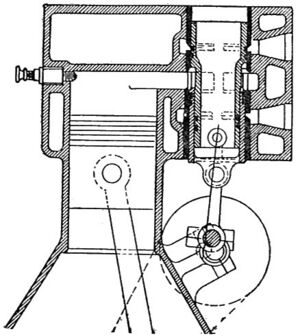
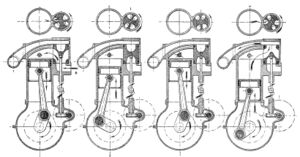
В двухтактных двигателях
Золотниковое газораспределение было применено ещё на двухтактном газовом двигателе Ленуара, считающемся первым в мире коммерчески успешным двигателем внутреннего сгорания (1859 г.). Его газораспределительный механизм с двумя коробчатыми золотниками был полностью скопирован с парораспределительного механизма паровых машин, причём при помощи золотников осуществлялся как впуск газовоздушной рабочей смеси, так и выпуск отработанных газов. Однако впоследствии развитие двухтактных двигателей пошло по пути использования поршневого (на лёгких двигателях) либо клапанного газораспределения.
Применение золотникового газораспределения на лёгких двухтактных двигателях современного типа (с кривошипно-камерной продувкой) прослеживается как минимум с 1920-х годов, однако по-настоящему удачная реализация этого принципа была осуществлена лишь в начале 1950-х годов восточногерманским инженером Даниэлем Циммерманом на спортивно-гоночных мотоциклах MZ, а затем в 1960-х — 70-х годах схожие решения стали появляться и на некоторых серийных мотоциклах марок Jawa, Yamaha, Suzuki, Kawasaki и других.
На двухтактных моторах с золотниковым управлением газораспределением для управления впуском используется золотник с приводом от коленчатого вала — вращающийся дискового или цилиндрического (кранового) типа либо имеющий возвратно-поступательное движение пластинчатого типа. Золотник тем или иным образом осуществляет открывание и закрывание впускного канала двигателя, управляя тем самым длительностью впуска. Благодаря этому удаётся сделать фазу впуска асимметричной относительно НМТ (как правило, начинается за 130—140° до НМТ и заканчивается за 40—50° после) и увеличить её длительность до 180—200°, тем самым улучшив наполнение цилиндра. Некоторые варианты реализации золотникового управления газораспределением позволяют даже изменять фазы газораспределения непосредственно во время работы двигателя. Выпуском как правило продолжает управлять поршень, открывающий выпускное окно (окна).
С аналогичной целью во впускном тракте двигателя может устанавливаться автоматически срабатывающий на перепад давления клапан лепесткового или мембранного типа (Yamaha и др.).
В начале 1950-х годов на пермском моторостроительном заводе № 19 под руководством В. В. Полякова были разработаны и выпущены небольшой серией двухтактные пятицилиндровые звездообразные авиамоторы ВП-760, ВП-1300 и ВП-2650 с газораспределением установленным в картере вращающимся золотником и продувкой двухступенчатыми поршнями в форме перевёрнутой буквы Т (узкая часть рабочая, широкая — нагнетательная), которые предназначались для применения в легкомоторной авиации[6].
Опыты с газораспределением вращающимся золотником велись в начале 1990-х годов фирмой Lotus применительно к двухтактному автомобильному двигателю с продувкой от приводного компрессора, причём, в отличие от обычного двухтактного двигателя с клапанно-щелевой продувкой, свежий воздух подавался в верхнюю часть цилиндра через золотник, а отработавшие газы удалялись через окна в нижней части цилиндра (у обычного двигателя с клапанно-щелевой продувкой воздух подаётся через окна в средней части цилиндра, а газы удаляются через клапан в головке блока). Золотник имел вид постоянно вращающегося вокруг своей оси полого цилиндра — ротора — с окнами в стенках, внутри которого располагался также имевший вид полого цилиндра статор с продольной перегородкой, поворот которого относительно ротора, осуществляемый электронной системой, управлял фазами газораспределения. Такое устройство газораспределения позволило вместо обычно используемого на дизелях с клапанно-щелевой продувкой непосредственного впрыска использовать более дешёвый вариант системы питания, с форсункой низкого давления, распыляющей топливо внутрь золотника, откуда рабочая смесь вдувалась внутрь цилиндра через впускное окно. Завершились эти работы безрезультатно, одной из причин чего было резкое ужесточение экологических стандартов в середине 1990-х годов (Евро-1, Евро-2 и т. д.), поставившее крест на использовании двухтактных двигателей на автомобильном транспорте.
В четырёхтактных двигателях
Золотниковое газораспределение с коробчатыми, поршневыми или вращающимися (крановыми) золотниками, так или иначе связанными с распределительным валом и осуществляющими открытие и закрытие впускных и выпускных окон, использовалось на некоторых четырёхтактных двигателях, но не получило широкого распространения из-за целого ряда трудностей на пути практической реализации данного принципа, в частности — проблемы с уплотнением золотников, особенно работающего на выпуск и в силу этого находящегося под большим давлением горячих отработанных газов.
Газораспределение коробчатым золотником, аналогичным золотникам паровых машин, было применено ещё на первом в мире четырёхтактном двигателе внутреннего сгорания, сконструированном Н. Отто (1861 г.), и достаточно широко использовалось на тихоходных стационарных двигателях XIX — самого начала XX века.
Управление газораспределением имеющими возвратно-поступательное движение поршневыми золотниками является фактически стандартным на паровых машинах и мощных поршневых насосах, некоторые конструкторы пытались приспособить его и к двигателю внутреннего сгорания, однако без большого успеха — перемещение золотника оказывалось весьма затруднено из-за большого давления газов, создававшего огромную силу трения между золотником и стенками золотниковой коробки, не говоря уже о проблемах с прорывом газов через уплотнения.
Несколько больший успех выпал на долю газораспределительных механизмов с вращающимся (крановым) золотником. Этот вариант газораспределения привлекал конструкторов благодаря бесшумности работы по сравнению с обычными тарельчатыми клапанами (стук которых при работе ГРМ был большой проблемой для двигателей начала XX века), возможности получить потенциально более высокую пропускную способность по сравнению с клапанным газораспределением и упростить ГРМ за счёт использования одного золотника на цилиндр, работающего и на впуск, и на выпуск, или даже одного на каждую пару цилиндров, а также устранить из камеры сгорания один из наиболее опасных очагов детонации — выпускной клапан (что, опять же, было весьма актуально в начале XX века, когда доступное топливо имело очень низкое октановое число).
Первый патент на газораспределение вращающимся золотником был получен британской фирмой Crossley[англ.] в середине 1880-х годов. Основанные на нём тихоходные газовые двигатели пользовались популярностью в качестве стационарных и выпускались этой фирмой с 1886 по 1902 год.
Пик популярности данной конструкции в автомобильных двигателях пришёлся на начало 1910-х годов, когда, следуя последней моде, свои варианты золотникового газораспределения представил целый ряд фирм, выпускавших дорогостоящие автомобили, таких, как Itala (Италия, 1911), Darraq (Франция, 1912), впоследствии Minerva (Бельгия, 1925).
Сравнительно удачные конструкции двигателей с газораспределением коническим вращающимся золотником создавались британцами Р. Кроссом и Ф. Аспином в 1930-х — 1950-х годах, находили применение на гоночных автомобилях, однако в массовое производство так и не попали, в том числе — из-за нерешённых проблем с уплотнением и смазкой золотника. В те же годы экспериментировал с золотниковым газораспределением германский инженер Ф. Ванкель в сотрудничестве с фирмами BMW, DVL, Daimler-Benz, Lilienthal и Junkers, однако, не добившись решительного успеха, он переключился на работу над проектом роторно-поршневого двигателя, в чём весьма преуспел.
В 1950-х годах в СССР были построены опытные двигатели с золотниковым газораспределением на базе серийных моторов «Москвич-400» (4-цил.) и ЗИС-120 (6-цил.), имевшие крановые золотники, установленные в головке блока и вращающиеся вокруг оси, параллельной оси коленчатого вала. По сравнению с нижнеклапанными, двигатели с золотниковым газораспределением имели лучшую наполняемость цилиндров и, соответственно, более высокую удельную мощность — например, на двигателе «Москвича» прибавка в мощности по сравнению с серийным составила 8 %. Однако при этом ощутимо увеличивался расход масла из-за проблем с уплотнением золотника, двигатель работал с заметным дымлением. Кроме того, в конце такта сжатия и во время рабочего хода поршня золотник испытывал большое трение из-за давления на него уплотняющего башмака, находящегося под давлением выхлопных газов, что значительно повышало потери на трение, а на шестицилиндровом двигателе даже привело к обрыву трёхрядной цепи привода ГРМ в ходе испытаний. Обеспечить требуемый моторесурс двигателям с золотниковым газораспределением так и не удалось[5].
Примерно тогда же британская фирма Norton выпустила некоторое количество гоночных мотоциклов с золотниковым газораспределением, но в 1954 году полностью прекратила работы в этом направлении. Разновидностью золотникового иногда считают гильзовое газораспределение, рассмотренное отдельно ниже по тексту.
С клапанным управлением газораспределением
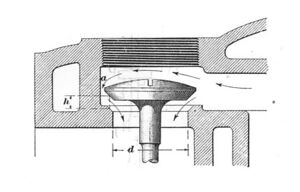
Управление газораспределением осуществляется при помощи тарельчатых клапанов, как правило имеющих привод от распределительного вала. Эта система наиболее распространена на современных четырёхтактных двигателях, а также мощных двухтактных (с клапанно-щелевой продувкой, имеются только выпускные клапана).
В данной конструкции ГРМ используется клапан, состоящий из тарелки (головки) и стержня (стебля), который служит для открытия и закрытия впускных и выпускных каналов. Главное преимущество тарельчатого клапана, позволившее ему достичь преимущественного распространения в данной области — простота обеспечения герметичности: под воздействием давления в камере сгорания его тарелка плотно прижимается к седлу, поэтому для исключения утечки газов вполне достаточно тщательно притереть эти детали друг к другу, причём усилие, создаваемое давлением в камере сгорания, направлено по оси стержня клапана и не мешает ему перемещаться вдоль направляющей. При открытии клапана он смещается относительно седла на расстояние, называемое высотой подъёма клапана. При этом открывается определённое проходное сечение, определяемое величиной высоты подъёма, размерами и формой клапана. В большинстве случаев впускные клапана имеют большее проходное сечение, чем выпускные, что объясняется высоким давлением отработавших газов и большей скоростью истечения в выпускных клапанах.
Ранее, примерно до 1950-х годов, клапаны обычно изготавливали из обычной углеродистой или низколегированной инструментальной стали (например, хромистой 40Х), однако по мере совершенствования двигателей и повышения их степени форсирования появилась необходимость применения как минимум для выпускных клапанов, температура которых может достигать 600—850 °С, специальных легированных жаростойких сталей, например сильхромовой (40Х10С2М / ЭИ107, 40Х9С2 / ЭСХ8), X45CrNiW189, X53CrMNi219, и т. п. Впускные клапана обычно имеют температуру не выше 300—400 °С и выполняются из хромистой, хромованадиевой или хромоникелевой сталей.
Иногда с целью удешевления из жаростойкой стали изготавливается только тарелка (головка) клапана, а стержень — из обычной инструментальной, также на тарелках выпускных клапанов иногда может производиться дополнительная наплавка слоя твёрдого жаростойкого сплава, повышающего срок службы клапана. В двигателях с большой тепловой напряжённостью камеры сгорания могут применяться клапана с полыми стержнями, заполненными натрием — при работе двигателя натрий плавится и, перемешиваясь, улучшает теплоотвод от клапана.
В последнее время могут использоваться клапана из титановых сплавов, сочетающие жаростойкость с лёгкостью, что позволяет уменьшить инерцию деталей ГРМ.
Ещё один метод борьбы с тепловой напряженностью выпускных клапанов — нанесение на тарелку керамического напыления, например оксида циркония. Эффект снижения рабочей температуры может составлять несколько сотен градусов.
Изготавливаются клапаны путём горячей высадки (объёмной штамповки) стального прутка, после чего подвергаются механической и термической обработке[5][7][8].
Тарелка (головка) клапана может иметь плоскую (Т-образную), выпуклую или тюльпанообразную (обтекаемую, с плавным переходом к стержню) форму. Клапана с выпуклой головкой иногда используются в качестве выпускных благодаря большой жёсткости и лучшей обтекаемости со стороны цилиндра, что особенно актуально в нижнеклапанном моторе. Тюльпанообразные клапана ранее часто устанавливались на впуске при большом диаметре клапана, так как считалось, что обтекаемая форма головки снижает сопротивление потоку воздуха, но впоследствии, примерно с 1980-х годов, от их использования отказались, так как они не давали значительного эффекта, или даже при той же величине подъёма ухудшали наполнение цилиндров по сравнению с обычными, при большей сложности изготовления.
Головка клапана имеет коническую рабочую поверхность — запорную фаску, плотно притёртую к ответной фаске седла (гнезда) клапана. Фаска на головке клапана выполняется под углом 30° или 45°. Фаска в 45° даёт меньшее проходное сечение при том же подъёме, чем фаска в 30°, однако облегчает центровку клапана в седле и способствует повышению его жёсткости, поэтому 30-градусная фаска применяется ограниченно, обычно на впускных клапанах высокофорсированных и спортивных двигателей. В некоторых случаях может применяться двойная фаска. Фаска подвергается шлифовке, а затем плотно притирается к седлу (гнезду). На нижнем (хвостовом) конце стержня клапана выполняются кольцевые проточки, предназначенные для крепления тарелок клапанных пружин, обычно осуществляемого при помощи конических сухарей (реже — поперечной шпилькой или на резьбе). Иногда для повышения срока службы клапана тарелка клапанной пружины оснащается упорным подшипником, допускающим свободное вращение клапана вокруг своей оси при работе двигателя. Ранее на хвостовой части стержня клапана иногда также выполняли кольцевую выточку под предохранительное кольцо, не дающее клапану провалиться в цилиндр, если лопнет его пружина или произойдёт случайное выпадение сухарей при работе двигателя[7][8].
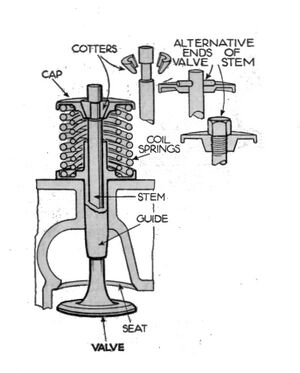
Сёдла (гнёзда) клапанов выполняются либо непосредственно в материале блока цилиндров (у нижнеклапанных моторов) или головки цилиндров, либо в виде запрессованных в них отдельных деталей из легированного чугуна, бронзы или жаростойкой стали (только выпускных клапанов, либо и впускных, и выпускных), иногда с наплавкой износостойкого кобальтового сплава типа сормайт[7]. Обычно седло имеет одну фаску с углом в 45°, или две фаски — верхнюю с углом в 30°, служащую переходом от основной фаски к стенке камеры сгорания, и основную в 45°. Иногда выполняется также нижняя фаска с углом порядка 60°, применение которой снижает сопротивление седла потоку воздуха. Особенное значение имеет проработка формы фаски сёдел впускных клапанов, через которые осуществляет наполнение цилиндров рабочей смесью[8].
Направляющие втулки клапанов служат для обеспечения их точной посадки в сёдла, изготавливаются из чугуна, алюминиевой бронзы или металлокерамических антифрикционных композиций (бронзографитовой и других). Для уменьшения расхода масла через зазор между направляющей клапана и его стержнем либо на сам стержень клапана одевается маслоотражательный колпачок из маслостойкой резины, либо на его направляющую устанавливается сальник с кольцевой пружинкой (маслосъёмный колпачок)[7][8].
Клапанные пружины обеспечивают закрытие клапана и его плотную посадку в седло, воспринимают усилия, возникающие при работе ГРМ. При сборке клапанного механизма пружина получает предварительную затяжку, величина которой является важным параметром, влияющим на качество работы двигателя. Если пружина в засухаренном состоянии не развивает должного усилия, указанного в технической документации — возникают отставание («подвисание») и подскакивание клапана при его закрытии, нарушающие фазы газораспределения и ухудшающие наполнение цилиндров горючей смесью, из-за чего двигатель не будет развивать полной мощности и не обеспечит паспортных динамических характеристик автомобиля. При полностью закрытом клапане остаточной силы пружины должно хватать для удержания контакта между кулачком распределительного вала и контактирующей с ним деталью ГРМ (толкателем, коромыслом, рокером), что позволяет сохранить заданную конструкторами продолжительность открытия клапана и устранить ударные нагрузки в приводе клапанов, быстро выводящие его из строя.
Как правило, клапанные пружины изготавливаются из легированной высокоуглеродистой стали (марганцовистой, кремнемарганцовистой, хромоникелеванадиевой) холодной навивкой с последующими термообработкой и дробеструйным наклёпом для повышения срока службы. Могут быть цилиндрическими или коническими, иметь постоянный или переменный шаг навивки. Для предотвращения износа опорной поверхности головки цилиндров и фиксации пружины под неё подкладываются стальные опорные шайбы[5][7][8][9].
Иногда применяются по две пружины на клапан, расположенные одна внутри другой, причём наружная и внутренняя пружина имеют разное направление витков для предотвращения заклинивания внутренней пружины витками внешней. Применение таких сдвоенных пружин позволяет несколько уменьшить габариты узла за счёт меньшей общей высоты двух пружин по сравнению с одинарной при том же усилии, а также служит в качестве страховки на случай поломки одной из пружин, тем самым повышая надёжность и безотказность работы двигателя. Также иногда клапанная пружина может устанавливаться не на самом клапане, а в толкателе (пример — дизель ЯАЗ-204)[7].
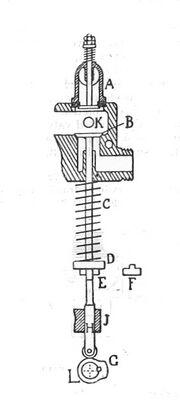
В большинстве случаев в клапанном механизме для управления клапанами используется выполненный из чугуна или легированной стали кулачковый распределительный вал, имеющий опорные шейки, служащие для установки вала в подшипниках его постели, и кулачки с различным профилем, определяющим фазы газораспределения двигателя. Обычно на один цилиндр приходится по два кулачка распределительного вала (один впускной и один выпускной), однако встречаются и иные варианты. Кроме того, распределительных валов может быть более одного. Привод распределительного вала осуществляется от коленчатого вала двигателя, причём у четырёхтактных моторов его частота обращения равна половине частоты обращения коленчатого вала, а у двухтактных — равна ей. Вал вращается в подшипниках скольжения, от осевого смещения удерживается обычно упорными полукольцами из стали, иногда с алюминиевым покрытием на рабочей поверхности, бронзы, антифрикционной металлокерамики или пластмассы.
В двигателях старого выпуска от распределительного вала часто осуществлялся привод других агрегатов двигателя — масляного и топливного насосов, прерывателя-распределителя зажигания, иногда даже стеклоочистителя. На современных двигателях топливный насос имеет электропривод, прерыватель-распределитель отсутствует и полностью заменён на электронную систему управления, а масляный насос обычно приводится непосредственно от коленчатого вала цепью или шестернёй.
В двигателях начала XX века иногда могли использоваться автоматически действующие впускные клапана, срабатывающие за счёт перепада давления между атмосферой и разрежением во впускном коллекторе, однако на высоких оборотах они работали неудовлетворительно, и вскоре вышли из употребления (выпускные клапана сохраняли привод от распредвала)[10].
Между кулачками распределительного вала и стержнями клапанов для передачи усилия устанавливаются передаточный звенья, конструкция которых зависит от типа газораспределительного механизма двигателя.
В двигателях с нижним расположением распределительного вала для снятия усилия с его кулачков используются толкатели, установленные в отверстия в блоке цилиндров, выполненные над постелью распредвала. От толкателя усилие может передаваться непосредственно на стержень клапана (в нижнеклапанных моторах) или через приводную штангу на приводящее в действие стержень клапана коромысло, меняющее направление усилия на противоположное (в верхнеклапанных моторах со штанговым приводом клапанов)[8].
Различают толкатели цилиндрические, тарельчатые (грибовидные) и роликовые. У первых двух типов опорная поверхность, находящаяся в контакте с кулачком распредвала, плоская либо сферическая, у роликовых толкателей же в контакте с кулачком распредвала находится ролик из твёрдой стали с высокими противоизносными свойствами, что позволяет значительно увеличить долговечность узла и снизить требования к противозадирным качествам смазочного масла — такая конструкция ранее применялась в основном на дизелях, но начиная с 1980-х годов получила широкое распространение. Толкатель с плоской или сферической опорной поверхностью для предотвращения преждевременного износа должен при работе вращаться вокруг своей вертикальной оси, что при плоской опорной поверхности достигается его смещением относительно оси кулачка, а при сферической — использованием кулачков со скошенной поверхностью[8].
В дизельных двигателях большого рабочего объёма иногда применяются качающиеся роликовые толкатели, представляющие собой качающийся рычажок с отверстием под ось с одного конца и находящимся в контакте с кулачком распредвала роликом с другого, усилие снимается с расположенной на рычажке сверху стальной пяты, на которую опирается штанга коромысла, что позволяет за счёт наличия у такого толкателя некоего передаточного отношения получить большое усилие, требуемое для привода газораспределительного механизма такого двигателя[8].
В современных моторах в толкателях часто размещают гидравлические компенсаторы клапанного зазора, в таком случае толкатели иногда называют гидравлическими. Они обеспечивают постоянный беззазорный контакт между деталями привода клапанов, что устраняет звук при работе двигателя и снижает износ благодаря устранению ударных нагрузок. Иногда гидрокомпенсаторы могут устанавливаться и внутри коромысел[8].
В двигателях с верхним расположением распределительного вала для привода клапанов используются либо рычаги (двуплечие или одноплечие), имеющие, в зависимости от конкретной конструкции, название коромысел или рокеров (рычажные толкатели), либо короткие цилиндрические толкатели, расположенные под распределительным валом, непосредственно между его кулачками и стержнями клапанов[8].
При работе двигателя, особенно под высокими нагрузками, стержень клапана удлиняется на бо́льшую длину, чем другие детали головки цилиндра, так как клапан испытывает дополнительную тепловую нагрузку за счёт омывания его тарелки, выступающей в камеру сгорания, горячими газами, в то время, как остальная головка цилиндров обычно имеет жидкостное охлаждение, и её температура не превышает 100…120°С (в двигателях с жидкостной системой охлаждения). При этом выбирается выставленный при регулировке двигателя тепловой зазор между клапаном и приводящей его деталью, в результате чего после прогрева двигателя ГРМ начинает работать практически бесшумно. При неправильной регулировке теплового зазора, перегреве клапана, износе фаски его головки или седла предусмотренный конструкцией двигателя тепловой зазор в приводе клапанов может отсутствовать, в результате чего клапана теряют герметичность и начинают прогорать[5].
В настоящее время большинство двигателей оснащаются системой автоматического регулирования теплового зазора в приводе клапанов, осуществляемого за счёт использования гидравлических компенсаторов клапанного зазора (в двигателях с приводом клапанов толкателями) или гидравлических упоров (в двигателях с рычажным приводом клапанов). Благодаря давлению масла, заполняющего внутреннюю полость гидравлического элемента, кулачок распределительного вала постоянно находится в контакте с передаточными звеньями ГРМ, что устраняет необходимость регулировки, а также повышает надёжность двигателя за счёт предотвращения возможности прогара клапана из-за износа его фаски или седла. После остановки двигателя на долгий срок масло из гидравлического элемента выдавливается, в результате чего после повторного пуска некоторые клапана могут издавать стук в течение нескольких минут. Длительность работы двигателя со стуком клапанов увеличивается по мере износа плунжерных пар гидрокомпенсаторов или гидроупоров. Кроме того, эти устройства чувствительны к вспениванию масла, поскольку при попадании внутрь плунжерной пары масла с воздухом она теряет работоспособность[5].
Классификация
Классификация газораспределительных механизмов двигателей с клапанным газораспределением осуществляется в зависимости от взаимного расположения самих клапанов и приводящего их распределительного вала, а также конструкции передаточных звеньев между ними.
По расположению клапанов выделяют двигатели:
- Нижнеклапанные (с боковым расположением клапанов);
- Верхнеклапанные (в старой литературе — «с подвесными клапанами») OHV;
- Со смешанным расположением клапанов.
По расположению распределительного вала выделяют двигатели:
- С распредвалом, расположенным в блоке цилиндров (с нижним распредвалом, Cam-in-Block);
- С распредвалом, расположенным в головке блока цилиндров (с верхним распредвалом, Cam-in-Head);
- Без распределительного вала.
По числу распределительных валов:
- с одним распредвалом на головку (обычно для двухклапанных цилиндров) SOHC;
- с двумя распредвалами, (для многоклапанных, отдельно для впускных и выпускных) DOHC.
По управлению газораспределением:
- с постоянными фазами;
- с управляемыми фазами.
По этим признакам клапанные механизмы четырёхтактных двигателей внутреннего сгорания разделяются на целый ряд подтипов.
Двигатели с распредвалом в блоке цилиндров
Нижнеклапанные
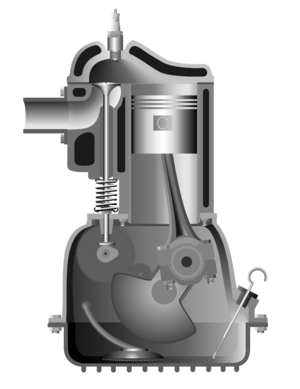
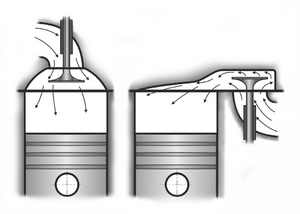
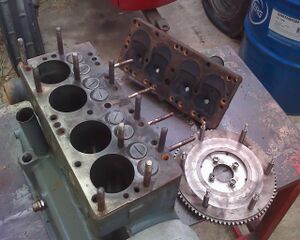
Нижнеклапанный двигатель (с боковым расположением клапанов, англ. L-Head, Flathead, SV — Side-Valve) — двигатель, у которого клапаны расположены в блоке цилиндров, тарелками вверх, и имеют привод от расположенного под ними распредвала посредством толкателей. В V-образных нижнеклапанных двигателях распредвал обычно расположен в развале блока цилиндров, клапана расходятся от него в виде буквы V.
Все детали ГРМ этого типа находятся внутри блока, что позволяет получить очень компактный двигатель. Распределительный вал находится в общем картере с коленвалом, что упрощает систему смазки и повышает безотказность, отсутствуют промежуточные передаточные звенья между кулачками распредвала и клапанами (коромысла, рокеры, рычаги и т. п.), нет необходимости в сложных уплотнениях стержней клапанов (маслосъёмные колпачки).
Головка блока нижнеклапанного мотора представляет собой простую чугунную или алюминиевую плиту с каналами для охлаждающей жидкости, она легко демонтируется, открывая удобный доступ к клапанам и поршням, что было весьма актуально в годы, когда поршни требовалось регулярно очищать от нагара, а клапаны — периодически притирать к сёдлам, для чего в их тарелках делались специальные шлицы для притирочной машинки.
Главный минус нижнеклапанной компоновки — обусловленная перевёрнутым расположением клапанов специфическая компоновка впускного и выпускного трактов, приводящая к снижению удельных характеристик двигателя. Из-за связанного с ней сложного пути бензовоздушной смеси, поток которой при входе в цилиндр резко меняет направление движения, повышается сопротивление на впуске и значительно ухудшается наполнение цилиндров, в особенности на высоких оборотах. Как следствие — в большинстве случаев нижнеклапанный двигатель получается тихоходным и неэкономичным, с низкой удельной мощностью[5].
Кроме того, конструктивные особенности нижнеклапанного двигателя резко ограничивают возможность повышения степени сжатия за счёт уменьшения объёма камеры сгорания, что обычно является наиболее простым и эффективным способом повышения удельной мощности двигателя внутреннего сгорания.[5]
Уменьшение высоты свода камеры сгорания с целью уменьшению её объёма в нижнеклапанном двигателе приводит к уменьшению проходных сечений впускного и выпускного трактов, причём в их наиболее критичной части, непосредственно прилегающей к камере сгорания, причиной чего является уменьшение зазора между стенкой камеры сгорания и тарелкой клапана. В результате по мере уменьшения объёма камеры сгорания и, соответственно, повышения степени сжатия, происходит ухудшение наполнения цилиндров, что значительно снижает эффективность данной меры форсировки двигателя. Отчасти устранить этот недостаток помогает использование поршней с выступающим в камеру сгорания вытеснителем, расположение сёдел клапанов в углублениях на поверхности блока и применение обращённой к клапанам лунки в днище поршня. Однако, даже с учётом этих мер, при степени сжатия порядка 8:1 и выше наполнение цилиндров нижнеклапанного двигателя ухудшается из-за эффекта дросселирования до такой степени, что делает дальнейшее повышение степени сжатия бессмысленным — полученное за счёт неё повышение эффективности рабочего процесса двигателя нивелируется ухудшением наполнения цилиндров. Кроме того, сама по себе форма камеры сгорания нижнеклапанного мотора препятствует увеличению диаметра тарелок и подъёма клапанов из-за их тесного расположения в камере сгорания, причём тем больше, чем выше степень сжатия двигателя, и, следовательно, тем компактнее камера сгорания его цилиндров.[9][11]
По той же причине не имеет смысла создание нижнеклапанного дизеля, поскольку в дизель-моторах для обеспечения эффективного рабочего процесса необходимы степени сжатия порядка 16:1 и выше.
Необходимость обеспечить, с одной стороны, минимальное конструктивно обусловленное расстояние между осями цилиндра и распределительного вала, а с другой — необходимый зазор между тарелкой клапана и стенками камеры сгорания, вынуждает конструкторов придавать камере сгорания нижнеклапанного двигателя сильно вытянутую форму. Поэтому не достигает значительного эффекта и уменьшение объёма камеры сгорания путём уменьшения её длины. Неоптимальная форма камеры сгорания, в свою очередь, значительно увеличивает теплоотдачу через стенки, вызывая потерю тепла и снижение КПД, увеличивает время горения смеси, что ограничивает быстроходность двигателя, а также способствует развитию детонации, из-за чего нижнеклапанный двигатель при той же степени сжатия требует более высокооктанового топлива, чем верхнеклапанный.
В незначительной степени эти недостатки могут быть устранёны наклоном осей клапанов относительно оси цилиндров, что уменьшает длину камеры сгорания, тем самым улучшая условия сгорания смеси и снижая склонность двигателя к детонации, а также снижает сопротивление потоку рабочей смеси, всасываемой в цилиндр (например, в двигателе автомобиля «Москвич-400» угол наклона клапанов составлял чуть более 8°), однако при этом быстро растут габариты двигателя, ограничивая возможности данного подхода в рядных двигателях[12].
В V-образном нижнеклапанном двигателе увеличивать угол наклона клапанов без чрезмерного роста наружных габаритов можно в значительно больших пределах, чем в рядном. Пытаясь преодолеть недостатки нижнеклапанной схемы, конструкторы иногда располагали клапана в блоке цилиндров V-образного нижнеклапанного мотора под очень большим углом к оси цилиндра, горизонтально или практически горизонтально, для чего распределительный вал приходилось размещать высоко в развале блока, а в привод клапанов вводить дополнительные звенья — длинные качающиеся толкатели (одноплечие рычаги) или коромысла (двуплечие рычаги). В частности, такую конструкцию ГРМ имел V-образный 8-цилиндровый двигатель Lycoming FB 1930-х годов, у которого клапана устанавливались под углом в 35° к оси цилиндра и приводились в действие через одноплечие рычаги. При таком расположении клапанов впускные и выпускные каналы примыкали к камере сгорания более плавно, без 90-градусного разворота, что позволило практически устранить проблемы, связанные с резким изменением направления движения заряда рабочей смеси на впуске, кроме того камера сгорания получалась сравнительно короткой.
Также дополнительным преимуществом данного конструктивного решения было то, что выпускные каналы удалось вывести вверх, а не внутрь развала блока, как на многих нижнеклапанных V8, что упростило конструкцию выпускной системы и снизило нагрев двигателя от выхлопных газов. Однако в полной мере сохранялись другие недостатки нижнеклапанных двигателей — малое проходное сечение впускного тракта и невозможность повышения степени сжатия выше определённого предела, а конструкция мотора с таким ГРМ оказалась очень сложной и дорогой в производстве, что помешало его распространению. По сути, данная компоновка ГРМ является «переходной» между нижнеклапанными двигателями и верхнеклапанными типа OHV (см. ниже). При дальнейшем увеличении угла наклона клапанов относительно оси цилиндров их уже приходилось переносить в головку цилиндров, тем самым делая двигатель верхнеклапанным.
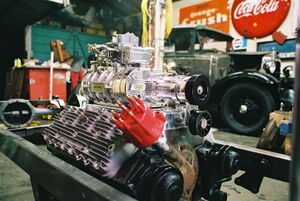
Наиболее же эффективный способ повышения удельной мощности нижнеклапанного двигателя — наддув от приводного нагнетателя или турбонагнетателя, что позволяет добиться хорошей наполняемости цилиндров и достаточно высокой эффективности рабочего процесса даже при невысокой степени сжатия. Однако из-за сложности и дороговизны реализации при сравнительно скромном по сравнению с двигателями других схем эффекте он применялся крайне нечасто, в основном в США 1930-е — 40-е годы, а также очень широко — в тюнинге американских нижнеклапанных V8 (в частности, на хотродах).
Камеры сгорания нижнеклапанного мотора имеют сложную форму и из-за этого как правило не подвергаются механической обработке, сохраняя шероховатую поверхность, полученную при отливке, что ещё больше снижает показатели двигателя и является причиной появления различий в объёме и, соответственно, характере работы камер сгорания одной головки. Длинные выпускные каналы, расположенные в блоке цилиндров, способствуют перегреву нижнеклапанного двигателя из-за дополнительного нагрева от горячих выхлопных газов. В особенности это касается нижнеклапанных V8, у которых как правило выпускные каналы проходят прямо сквозь блок цилиндров в поперечном направлении, из развала блока наружу к выпускным коллекторам, и проходящие через них выхлопные газы по пути отдают много тепла, вызывающего перегрев двигателя, в особенности при недостаточной эффективности системы охлаждения.
На некоторых нижнеклапанных двигателях штатная регулировка клапанного зазора вообще не была предусмотрена (Ford T, Ford A и их производные), в случае серьёзного нарушения работы стержни клапанов дорабатывали: при слишком малом зазоре немного подпиливали (торцевали), а при слишком большом — расковывали утолщённую хвостовую часть, при этом слегка удлиняя стержень. Впоследствии на большинстве двигателей был введён механизм регулировки зазоров (закрученный в толкатель болт с контргайкой), однако доступ к нему зачастую был крайне неудобен (впрочем, требовался он на таких моторах сравнительно редко). Полностью данную проблему решают гидравлические компенсаторы клапанного зазора, встроенные в токатели.
Вплоть до 1950-х годов благодаря своей простоте и дешевизне двигатели с таким ГРМ были наиболее распространены на легковых (за исключением спортивных) и грузовых автомобилях. Первые массовые модели с верхнеклапанными двигателями появились ещё в 1920-х годах, однако в те годы нижнеклапанные моторы конкурировали с ними практически на равных. Лишь к 1950-м годам, после появления в широком доступе топлива с более высокими октановыми числами, реализация преимуществ которого требовала повышения степени сжатия, стало очевидно, что нижнеклапанная схема сдерживает развитие автомобилестроения, мешая созданию более совершенных, динамичных и скоростных автомобилей, соответствующих изменившимся условиям дорожного движения. В результате в первой половине 1950-х годов на легковых автомобилях началось массовое внедрение верхнеклапанных двигателей, лишённых присущих нижнеклапанной схеме недостатков. На отдельных моделях легковых автомобилей, впрочем, нижнеклапанные двигатели продержались до начала 1960-х годов (все модели Plymouth в варианте с рядной шестёркой, Studebaker, Rambler, Simca Vedette, ЗИМ ГАЗ-12), а на грузовых автомобилях эта схема вообще использовалась вплоть до семидесятых годов, если не дольше — например, грузовики ГАЗ-52 и ЗИЛ-157 с нижнеклапанным мотором выпускался до 1990-х годов. В спецтехнике нижнеклапанные двигатели широко используются и в наши дни.
Кроме того, нижнеклапанные двигатели сохраняют определённую популярность в поршневой малой авиации, где их низкие рабочие обороты оборачиваются большим достоинством, так как позволяют устранить из конструкции понижающий редуктор привода на винт. Так, можно отметить бельгийские оппозитные нижнеклапанные авиамоторы D-Motor LF26 и LF39, которые свою максимальную мощность выдают при частоте обращения коленчатого вала всего лишь в 2800…3000 об./мин. Простота конструкции, надёжность и безотказность нижнеклапанного мотора также являются большими преимуществами в данной области.
С двухрядным расположением клапанов
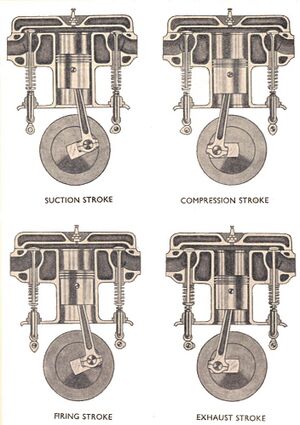
Разновидностью схемы с нижним расположением клапанов были имевшие некоторое распространение в первой половине XX века двигатели с Т-образной головкой (T-head в англоязычной литературе), или нижнеклапанные с двухрядным расположением клапанов. В них впускные клапаны находились с одной стороны блока цилиндров, а выпускные — с другой. Распределительных валов также было два. Такими двигателями, в числе прочих, оснащались первые «Руссо-Балты».
Цель данной конструкции — устранить перегрев впускных клапанов и впускных каналов в блоке за счёт изоляции их от раскалённых выпускных. Дело в том, что низкооктановый бензин, доступный в начале XX века, отличался высокой склонностью к детонации, что делало применение этой схемы в какой-то мере выгодным — более холодная бензовоздушная смесь имеет несколько более высокое октановое число (на этом же принципе работал впрыск воды в цилиндры, охлаждавшей рабочую смесь — конструкция, также имевшая хождение в те годы). В остальном двигатель с такой системой газораспределения имел худшие характеристики, чем имеющий обычный нижнеклапанный ГРМ, в частности — имел меньшую удельную мощность. Кроме того, он получался сложным, громоздким, тяжёлым и дорогим в производстве. Поэтому после Первой мировой войны, отмеченной значительным прогрессом как в области моторостроения, так и в нефтехимии, данная схема ГРМ вышла из употребления.
Данная схема также позволяет в нижнеклапанном двигателе применить три-четыре клапана на цилиндр — два впускных с одной стороны и один-два выпускных с другой, однако в случае нижнеклапанного мотора получаемый за счёт этого выигрыш невелик.
Со смешанным расположением клапанов (тип IOE)
Также встречаются обозначения F-Head или IOE (Intake Over Exhaust — «впускной клапан над выпускным»). У такого двигателя обычно впускные клапаны находятся в головке блока, как у верхнеклапанного мотора, и приводятся в действие при помощи штанг толкателей, а выпускные — в блоке, как у нижнеклапанного двигателя. Распределительный вал был один и был расположен в блоке, как у обычного нижнеклапанного мотора.
Эта схема обладает тем преимуществом, что её мощность ощутимо выше, чем у «чистого» нижнеклапанного — верхнее расположение впускных клапанов позволяет ощутимо улучшить наполнение цилиндров рабочей смесью. Как правило, такие двигатели переделывались из нижнеклапанных в качестве меры текущей модернизации, что зачастую было технологически проще и экономически выгоднее перехода к полностью верхнеклапанному мотору на основе того же блока цилиндров.
Такие двигатели широко применялись фирмами Rolls-Royce и Rover (включая внедорожники Land Rover) благодаря их высокой надёжности как по сравнению с нижнеклапанными (из-за хорошего охлаждения верхних клапанов), так и по сравнению с ранними верхнеклапанными двигателями (из-за вдвое меньшего числа штанг), а также способности работать на низкооктановом бензине без детонации.
Подобные «полуверхнеклапанные» переделки на базе серийных моторов существовали и в СССР — это были спортивные двигатели на базе агрегатов автомобилей «Москвич», «Победа» и ЗИМ. Выигрыш в мощности, в сочетании с иными мерами форсировки, был значительным — до 20…40 л. с., при исходной мощности самих указанных двигателей в 35, 50 и 90 л. с., соответственно. Планировалось использование подобного мотора на наследнике «Победы», однако в итоге выбор был сделан в пользу полноценного верхнеклапанного мотора полностью нового семейства.
С широким распространением «настоящих» верхнеклапанных двигателей, эта схема почти полностью вышла из употребления. Тем не менее, последний такой двигатель был выпущен фирмой Willys в 1970-х годах.
В очень редких случаях (мотоциклы Indian Four 1936 и 1937 годов выпуска) верхними делались выпускные клапана, а впускные — оставались нижними. Эта конструкция оказалась крайне неудачной из-за постоянного прогара выпускных клапанов, и более не повторялась.
Верхнеклапанные со штанговым приводом клапанов (тип OHV)
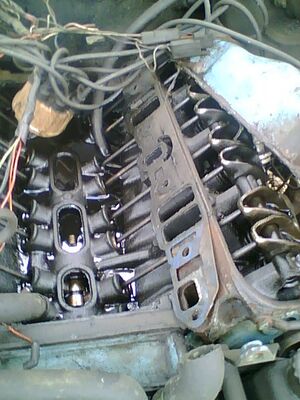

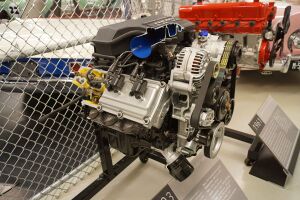
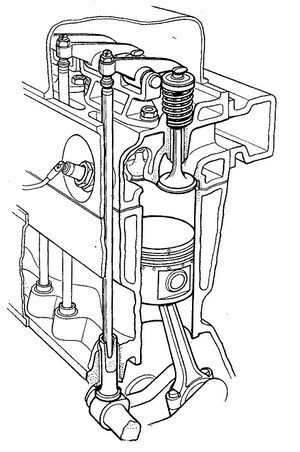
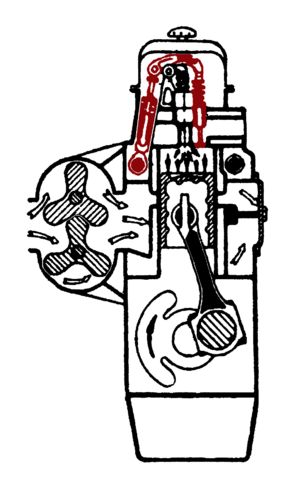
Данная конструкция ГРМ была изобретена Дэйвидом Данбаром Бьюиком (David Dunbar Buick) в самом начале XX века. У двигателей с таким ГРМ клапаны расположены в головке цилиндров, а распредвал — в блоке (англоязычное обозначение — OHV, OverHead Valve; также встречается I-Head, или Pushrod, то есть, «со штангами толкателей»). Разнесённые далеко друг от друга распределительный вал и клапаны вынуждают устанавливать между ними длинные передаточные звенья — штанги толкателей, передающие усилие от контактирующих с кулачками распредвала толкателей на коромысла, непосредственно приводящие в движение клапаны, что и является главной отличительной особенностью данной схемы ГРМ.
Клапаны в головке цилиндров как правило расположены в один ряд, вертикально (при плоскоовальной камере сгорания) или с небольшим наклоном (при клиновой камере сгорания), примерно на продольной оси камеры сгорания, однако встречаются и иные варианты. Так, на двигателях HEMI V8 концерна Chrysler камера сгорания полусферическая, впускные и выпускные каналы подходят к ней по радиусам полусферы — соответственно, впускные и выпускные клапана расположены в два ряда по разные стороны от продольной оси камеры сгорания, с большим наклоном, а приводящие их штанги толкателей расходятся от расположенного в развале блока распределительного вала в виде буквы V (по два ряда штанг на каждую головку V-образного мотора — верхний ряд приводит впускные клапана, нижний выпускные). На рядном четырёхцилиндровом двигателе GM 122 / Vortec 2200 и некоторых моторах семейства GM Big Block V8, вроде Vortec 8100, с диагонально ориентированной клиновой камерой сгорания, клапана также располагались в два ряда с наклоном и также приводились от V-образно расположенных штанг толкателей. И в том, и в другом случае применение усложнённой компоновки ГРМ объясняется желанием конструкторов спроектировать впускные и выпускные каналы с более эффективной с точки зрения пропускной способности конфигурацией.
Иногда распределительный вал по компоновочным соображениям располагают не в полости картера двигателя, рядом с коленчатым валом, а намного выше, непосредственно под головкой цилиндров, при этом сохраняются приводящие коромысла клапанов короткие штанги толкателей. Примером такого решения являются двухтактные дизели семейства ЯАЗ-204 / 206 (Detroit Diesel 4-71 / 6-71), причём привод распределительного вала (а также расположенного симметрично ему уравновешивающего вала) в них осуществлялся через сложную систему шестерён, расположенных со стороны маховика. В данном случае причиной такого расположения распредвала было то, что эти двигатели оснащались приводным компрессором, который устанавливался непосредственно на боковую стенку блока и осуществлял продувку цилиндров через расположенные в их средней части окна (см. ниже), так что выполненные в блоке цилиндров каналы для прохода воздуха попросту не оставляли места для распредвала, толкателей и штанг, ввиду чего их пришлось расположить выше.
Подобная «полуверхневальная» конструкция изредка применяется также на легковых автомобильных и мотоциклетных двигателях, например — французском Renault Cléon-Alu (Moteur A) 1960-х — 80-х годов с одним «полуверхним» распредвалом высоко в блоке, приводящим наклонно расположенные в головке клапана, или некоторых двухцилиндровых оппозитных мотоциклетных моторах фирмы BMW, включая выпускающий до сих пор BMW R nineT, у которых два распределительных вала с цепным приводом расположены очень близко к головкам, но всё же сохраняются очень короткие штанги толкателей. Выгода здесь состоит в уменьшении массы и, соответственно, инерции механизма привода клапанов по сравнению с обычным вариантом ГРМ типа OHV, что позволяет повысить рабочие обороты, приблизившись по характеристикам к верхневальным моторам, при этом на рядном двигателе сохраняется один распределительный вал. Однако привод распределительного вала получается сложнее и менее надёжным.
В очень редких случаях клапана могут располагаться в головке цилиндров не вертикально или под небольшим наклоном, а горизонтально или почти горизонтально. В этом случае для их привода от расположенного в блоке распредвала (распредвалов) используются непосредственно рычаги или коромысла, без приводных штанг. Так, у рядных авиамоторов Duesenberg Aero с четырьмя клапанами на цилиндр, некоторых автомобильных двигателей той же фирмы (вместе также известных как Duesenberg Walking Beam Engines), а также моторах фирмы Lanchester, для привода клапанов, расположенных в два ряда справа и слева от камеры сгорания, использовались установленные на боковых стенках блока цилиндров очень длинные коромысла, нижняя часть которых находилась в контакте непосредственно с кулачками распределительных валов, а верхняя — приводила клапана.
Иногда считается, что такая конструкция была впервые применена на двигателе автомобиля Cameron в 1906 году. В V-образных двигателях компоновка с расположенными в головках цилиндров горизонтально или практически горизонтально клапанами и одним распределительным валом высоко в развале блока была применена на авиационных двигателях времён Первой мировой войны Lancia Tipo 4 и Tipo 5 конструкции Винченцо Лянча, а также V-образном 12-цилиндровом моторе Lycoming BB[13][14][15].
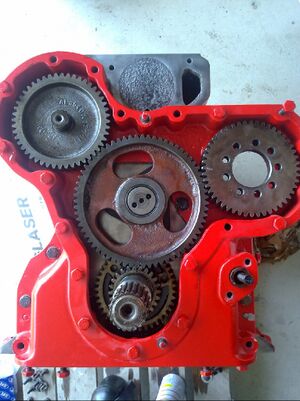
Положительная сторона ГРМ типа OHV — относительно простая конструкция и обеспечиваемая ей конструктивная надёжность, в частности, как правило используется простой и надёжный привод распределительного вала шестернями, что исключает саму возможность таких неисправностей, как разрыв ремня ГРМ или «перескакивание» цепи в механизме с цепным приводом (реже используется короткая пластинчато-зубчатая цепь Морзе, позволяющая достичь полной бесшумности привода, но из-за малой длины риск её растяжения намного ниже, чем при верхнем расположении распредвала; ременной привод используется лишь в виде исключения, например — на некоторых японских дизелях). Эксплуатационные нагрузки на детали ГРМ также оказываются сравнительно невысокими, чем обеспечивается высокая долговечность и нетребовательность к смазочным материалам. В V-образном двигателе данная схема газораспределения имеет дополнительное преимущество в том, что появляется возможность осуществить привод клапанов обеих головок от единственного распределительного вала, расположенного в развале блока.
Многие двигатели с ГРМ типа OHV ощутимо более компактны по сравнению с верхневальными, так как у них отсутствует расположенный сверху в головке блока распределительный вал, что особенно актуально для двигателей без оси коромысел, у которых каждое коромысло опирается на отдельную опорную стойку в виде шпильки с полусферическим сегментом (ball seat), что характерно для американских двигателей; для рядных двигателей это в особенности касается габарита по высоте, а для V-образных — и высоты, и габаритной ширины.
Спортивные двигатели с ГРМ типа OHV могут успешно работать и на 9,5 тыс. об/мин (NASCAR), или даже 10…12 тыс. об/мин (NHRA Pro Stock), но для обеспечения этого требуются специальные, весьма дорогостоящие конструктивные и технологические решения (очень жёсткие, и при этом лёгкие, титановые штанги толкателей, специальные распредвалы с большим диаметром шеек, клапанные пружины, коромысла, и так далее); к примеру, стоимость постройки двигателя уровня NHRA Pro Stock — порядка $100 000, и при этом он практически не имеет общих деталей со взятым за основу серийным двигателем. Поэтому как правило двигатели этой схемы сравнительно низкооборотные, но при этом с хорошей эластичностью и гибкой моментной характеристикой[источник не указан 2161 день].
Кроме того, такая схема затрудняет использование более двух клапанов на цилиндр (двигатели с таким ГРМ, имеющие 4 клапана на цилиндр, имеют большие габариты и массу, что делает их малоприменимыми в легковых автомобилях, но вполне приемлемыми для грузовиков и тяжёлой техники — примеры тому двигатели КамАЗ, ЯМЗ, ТМЗ, дизель тепловоза ЧМЭ3 и многие другие) и усложняет проектирование впускных и выпускных окон в головке цилиндров с высокоэффективной с точки зрения пропускной способности и сопротивления потоку конфигурацией.
В СССР первым массовым верхнеклапанным мотором на легковом автомобиле стал двигатель «Волги» ГАЗ-21 (малосерийные НАМИ-1 и ЗИС-101 имели такой ГРМ уже в 1920-х — 30-х годах). Из советских автомобилей такой механизм газораспределения имели все массовые карбюраторные модели «Волги», «Москвичи» семейств М-407, М-408 и М-2138, а также грузовики и автобусы с карбюраторными двигателями конфигурации V8 (ЗИЛ, ГАЗ). В настоящее время в России производятся рядные четырёхцилиндровые двигатели семейства УМЗ-4216 (а до конца 2021 года также производился V8 ЗМЗ-523 семейства ЗМЗ-53), имеющие штанговый привод клапанов и инжекторную систему питания, позволившую им вписаться в рамки экологического стандарта Евро-5. Также ГРМ со штанговым приводом клапанов имели практически все массово выпускавшиеся в СССР быстроходные дизельные двигатели, в частности, ЯАЗ-204/206, ЯМЗ-236/238, КамАЗ-740, и так далее (исключение составляют дизели семейства В-2).
В мировой практике легкового автомобилестроения такие двигатели достаточно широко использовались ещё с 1910-х — 1920-х годов, однако вплоть до появления в конце 1940-х — первой половине 1950-х годов высокооктанового топлива в широком доступе не могли достичь решительного превосходства над нижнеклапанными, так как при сравнимой мощностной отдаче последние имели преимущества в отношении простоты конструкции и дешевизны производства. Так, в США «Форд» и «Крайслер» на своих довоенных моделях использовали только нижнеклапанные моторы, GM — как верхнеклапанные, так и нижнеклапанные, причём вполне сравнимые между собой по мощности и другим характеристикам. В довоенной Германии верхнеклапанные моторы имели большее распространение, но наряду с этим продолжался и массовый выпуск нижнеклапанных.
Повсеместное распространение верхнеклапанных моторов началось после появления в 1949 году двигателя Oldsmobile Rocket V8 со степенью сжатия, рассчитанной на высокооктановое топливо, спровоцировавшего в американской автомобильной промышленности «гонку лошадиных сил», не утихавшую вплоть до начала 1970-х. В Европе двигатели со штанговым приводом клапанов надолго не задержались и по сути стали переходным вариантом от нижнеклапанных к верхневальным — уже к концу 1960-х годов эта схема там стала считаться устаревшей и достаточно редко использовалась на новых моделях легковых автомобилей. Однако в США, где вплоть до недавнего времени были популярны сравнительно малооборотные двигатели большого рабочего объёма, для которых штанговый привод клапанов является вполне целесообразным, газораспределительный механизм типа OHV очень широко использовался вплоть до 1980-х и даже 1990-х годов, и продолжает встречаться в настоящее время на современных легковых двигателях — примером может послужить выпускающийся с 2003 года Chrysler 5.7 L Hemi (Dodge Ram, Dodge Charger R/T, Jeep Grand Cherokee, Chrysler 300C), использующий технологию динамически изменяемого рабочего объёма и динамического изменения фаз газораспределения.
Иногда такие двигатели использовались и на недорогих современных европейских автомобилях из-за своей дешевизны и компактности. Например, Ford Ka первого поколения (1996—2002) использовал инжектированную версию четырёхцилиндрового двигателя Kent разработки конца пятидесятых годов с ГРМ типа OHV, имеющую весьма компактные по современным стандартам размеры, что позволило уместить двигатель в небольшом моторном отсеке Ka.
В моторах грузовиков и тяжёлой техники, для которых меньшее число рабочих оборотов и инерционность ГРМ не является недостатком, а надёжность и долговечность первостепенны, ГРМ типа OHV всё ещё очень широко распространён. Схема OHV популярна и на малооборотистых четырёхтактных двигателях для газонокосилок, бензиновых электростанций, мотоблоков. Современные тракторные двигатели также имеют указанную схему.
Ещё одно применение двигателей такой схемы — классические американские мотоциклы, в первую очередь Harley-Davidson и indian, а также мотоциклы некоторых японских производителей, подражающих им, например Yamaha (под брендом Star) и Kawasaki Heavy Industries. Надёжность и эластичность таких моторов, вместе с повышенной в сравнении с другими компоновками ГРМ вибро- и шумонагруженностью давно стали отличительной чертой мотоциклов в классическом американском стиле[источник не указан 2250 дней].
Двигатели с распредвалом в головке цилиндров (OHC)
SOHC
Двигатель с одним верхним распределительным валом и клапанами в головке (Overhead Camshaft или SOHC — Single OverHead Camshaft). Одним из первых был применён в 1910 году британской фирмой Maudslay на модели 32 HP.
-
Привод клапанов коромыслами
-
Привод клапанов рычагами (рокерами)
-
Привод клапанов толкателями
-
Смешанный привод клапанов — толкателем и коромыслом
В зависимости от конкретной конфигурации привода клапанов, выделяют двигатели с приводом клапанов коромыслами, рычагами (рокерами) или цилиндрическими толкателями.
В верхневальных двигателях с приводом клапанов коромыслами для привода клапанов используются коромысла — двуплечие рычаги, один из концов которых (обычно более короткий) находится в контакте с расположенным под ним кулачком распредвала, а второй (более длинный) — со стержнем клапана. В большинстве случаев коромысла расположены на общей оси, что облегчает сборку и разборку газораспределительного механизма. Такой привод клапанов обычно применяется на двигателях с полусферической или шатровой камерой сгорания, которые требуют расположения клапанов двумя рядами в виде буквы V, и в которых при использовании других типов привода клапанов пришлось бы использовать либо очень длинные рычаги, либо два распределительных вала, по одному на каждый ряд клапанов, что как правило является менее предпочтительным. Хотя, в принципе, ничто не мешает использовать привод клапанов коромыслами и при однорядном расположении клапанов. Кроме того, благодаря расположению распределительного вала ниже коромысел головка блока получается сравнительно компактной по высоте (но зато имеет большую ширину). Примеры верхневальных двигателей с приводом клапанов коромыслами — «Москвич-412» (полусферическая камера сгорания), некоторые модели двигателей фирм BMW (полусферическая) и Honda (шатровая), 8-клапанный мотор Renault Logan (шатровая).
В верхневальных двигателях с приводом клапанов рычагами (рокерами) в качестве передаточного звена между кулачками распределительного вала и клапанами используются одноплечие рычаги (рычажные толкатели), опирающиеся на общую ось или на индивидуальные опорные стойки (упоры) в виде болта со сферической рабочей поверхностью, к которой рычаг прижимается силой специальной шпилечной пружины. Распределительный вал расположен над рычагами и толкает их примерно посередине. Данная схема сравнительно проста в реализации и дешева, однако имеет повышенный уровень шумности, а поверхность контакта кулачка распределительного вала и рычага испытывает большие нагрузки, что требует высоких противозадирных характеристик смазочного масла. Кроме того, из-за расположения распределительного вала над рычагами головка цилиндров получается громоздкой по высоте (ширина зависит от конкретной компоновки, но в целом больше, чем при приводе клапанов цилиндрическими толкателями). Такой ГРМ характерен для двигателей «Жигулей» ВАЗ-2101…2107 и «Нивы» ВАЗ-2121, а также ряда других двигателей, преимущественно разработки 1960-х — 70-х годов.
В верхневальных двигателях с приводом клапанов цилиндрическими толкателями распределительный вал расположен непосредственно над стержнями клапанов и приводит их посредством коротких цилиндрических толкателей. Механизм привода получает очень простым и с минимальной инерцией деталей, что выгодно для высокооборотных двигателей, а головка цилиндров — достаточно компактной по всем направлениям. Однако регулировка клапанного зазора при такой конструкции привода клапанов вызывает значительные затруднения из-за затруднённого доступа к толкателям, поэтому современные моторы с таким ГРМ обычно имеют гидрокомпенсаторы клапанного зазора, встроенные в толкатели. Благодаря указанным выше преимуществам (простота, компактность, минимальная инерция) в настоящее время данный тип привода клапанов является наиболее распространённым на легковых автомобильных двигателях (как SOHC, так и DOHC).
На одном моторе могут применяться сразу несколько типов привода клапанов — так, в двигателе Triumph Dolomite Sprint с четырьмя клапанами на цилиндр впускные клапаны приводились через толкатели, а выпускные — через рокеры, причём от одного и того же кулачка на единственном распределительном валу.
В большинстве случаев схема OHC ассоциируется с двигателями, имеющими по два клапана на цилиндр, но в некоторых моторах могут применяться по три или даже четыре клапана на цилиндр с приводом от одного верхнего распредвала. Например, на V-образном восьмицилиндровом моторе Mercedes-Benz M113 в каждой головке цилиндров был установлен распределительный вал, от кулачков которого приводились коромыслами по два впускных клапана и один большой выпускной (три кулачка на каждый цилиндр). Иногда используются коромысла в форме буквы Y, позволяющие от одного кулачка распредвала приводить сразу два клапана (Subaru EJ25). В настоящее время такие моторы практически полностью вытеснены моторами с ГРМ типа DOHC.
Схема OHC была наиболее распространена во вторую половину шестидесятых — восьмидесятые годы. Целый ряд двигателей такой схемы выпускается и в наше время, преимущественно для недорогих автомобилей (скажем, ряд двигателей Renault Logan).
DOHC
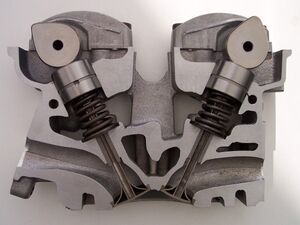
Двигатель с двумя распредвалами в головке цилиндров (Double OverHead Camshaft). Существуют две серьёзно различающиеся разновидности этого механизма, отличающиеся количеством клапанов.
2OHC / DOHC с двумя клапанами на цилиндр
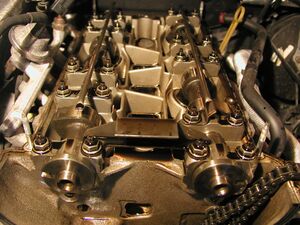
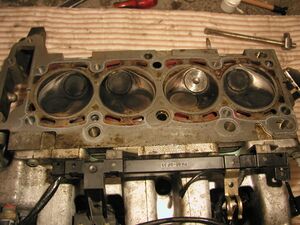
Эта схема является усложнённой разновидностью обычной OHC. В головке блока цилиндров расположены два распредвала, один из которых приводит впускные клапаны, второй — выпускные, при этом на каждый цилиндр приходится один впускной и один выпускной клапан. Эта схема применялась в 1960-х — 1970-х годах на высокопотенциальных двигателях таких автомобилей, как Fiat 125, Jaguar, Alfa Romeo, а также опытном двигателе гоночных автомобилей «Москвич-412Р», «Москвич-Г5» и в легковых автомобилях, также лёгких коммерческих, концерна Ford для европейского рынка, вплоть до 1994 года.
Схема позволяет значительно увеличить количество оборотов коленчатого вала за счёт уменьшения инерции привода клапанов, следовательно, увеличить мощность, снимаемую с двигателя. Например, мощность спортивной модификации двигателя «Москвича-412» с двумя распределительными валами объёмом 1,6 литра составляла 100—130 л. с.
DOHC с тремя и более клапанами на цилиндр
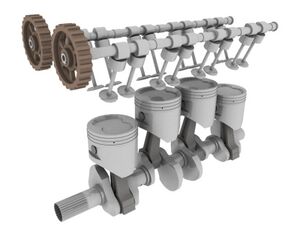
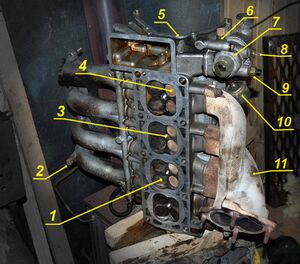
Два распредвала, каждый из которых приводит свой ряд клапанов. Как правило, один распредвал толкает два впускных клапана, другой — один или два выпускных. В настоящее время как правило используются четыре клапана на цилиндр, то есть, фактически, двухрядный вариант схемы OHC со вдвое большим количеством распредвалов и клапанов, однако могут осуществляться и иные схемы с общим количеством клапанов на цилиндр от трёх до шести. Привод клапанов, как правило, цилиндрическими толкателями, как наиболее компактный. В большинстве случаев используется шатровая камера сгорания, хотя существует и вариант с полусферической камерой сгорания, в которой все четыре клапана установлены наклонно в разных плоскостях — при этом сильно усложняется конструкция привода клапанов, поэтому распространения данная конструкция не получила.
Данная схема ГРМ позволяет значительно повысить удельную мощность двигателя за счёт лучшего наполнения цилиндра, особенно на высоких оборотах. Применение нескольких маленьких впускных клапанов вместо одного большого позволяет не только увеличить их общее проходное сечение, но и снизить динамические нагрузки, возникающие в приводе клапанного механизма, благодаря уменьшению массы каждого клапана и его рабочего хода, а следовательно — снизить инерцию деталей ГРМ и повысить рабочие обороты двигателя. На выпуске применение двух маленьких клапанов вместо одного большого позволяет снизить их температуру за счёт улучшения теплоотвода при малом диаметре тарелки клапана[5].
Однако такой двигатель из-за быстрого очищения цилиндра более чувствителен к длительности фазы перекрытия клапанов (когда открыты одновременно впускные и выпускные клапаны) — при высокой скорости длительность фазы должна быть больше для лучшей очистки цилиндров, однако на низких оборотах это приводит к потерям заряда горючей смеси и снижению эффективности работы. Иными словами, двигатель с таким ГРМ обычно имеет слабую тягу «на низах» и требует поддержания высоких оборотов для интенсивного разгона. Радикальным решением данной проблемы является применение изменяемых фаз газораспределения (см. ниже).
Сама по себе данная схема ГРМ известна как минимум с 1920-х годов, но длительное время она применялась только на авиационных моторах и двигателях спортивно-гоночных автомобилей, например Duesenberg Model J. Также ГРМ с четырьмя клапанами на цилиндр и двумя верхними распределительными валами оснащались некоторые танковые двигатели, в частности — знаменитый танковый дизель В-2 (Т-34, КВ, ИС) и американский бензиновый V8 Ford GAA («Шерман» M4A3), причём оба изначально разрабатывались в качестве авиационных. В массовом автомобилестроении данная компоновка стала востребована лишь в 1980-х годах, когда возможности традиционной схемы ГРМ с одним верхним распределительным валом с точки зрения мощностной отдачи оказались, несмотря на все ухищрения конструкторов, близки к исчерпанию.
Двигатели с двумя верхними распределительными валами и четырьмя клапанами на цилиндр применяются на большей части выпускаемых в настоящее время легковых автомобилей, в частности — семейство двигателей ЗМЗ-406, ЗМЗ-405 и ЗМЗ-409, устанавливаемых на автомобилях «Газель» (ранее) и УАЗ (до 2008-го года также «Волга»), или моторы ВАЗ-2112 и его модификации, устанавливаемые на современных моделях ВАЗ.
Стоит отметить, что существуют двигатели с четырьмя клапанами на цилиндр, не принадлежащие к схеме DOHC, например — дизельные моторы Cummins с четырьмя клапанами на цилиндр (устанавливаются на автомобили Группы ГАЗ), в которых привод всех клапанов осуществляется от единственного распределительного вала через коромысла с крейцкопфами. Точно так же, существовали двигатели с двумя распределительными валами, но всего двумя клапанами на цилиндр.
Привод распределительного вала
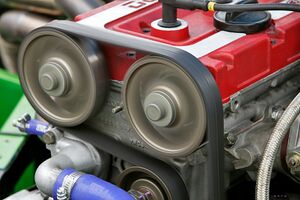
Приводы ГРМ по типу делятся на:
- ременные;
- цепные;
- шестеренчатые;
- комбинированные.
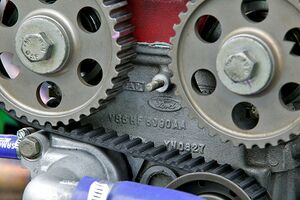
Распредвалы двигателей, выполненных по схеме SOHC или DOHC, приводятся в движение зубчатым ремнём или цепью, причём конструктивная реализация привода при данных схемах газораспределения существенно затруднена из-за верхнего расположения распределительного вала (валов), на значительном удалении от коленвала, что обуславливает большую длину передаточного звена между ними.
Привод распредвалов зубчатым ремнём начиная с 1980-х годов стал наиболее распространенным на легковых автомобилях. Зубчатый ремень находится вне объёма, омываемого маслом, попутно ремень приводит в движение водяной насос. Назначение зубьев — обеспечивать хорошее сцепление и исключать проскальзывание. Их количество строго определено, так как от того зависит синхронизация коленвала и распредвалов.
Преимущества привода зубчатым ремнём — дешевизна, бесшумность, практически полное отсутствие у ремня склонности к растягиванию, возможность обеспечить привод от одного ремня обоих распредвалов (в схеме DOHC) и большого количества вспомогательных агрегатов (насоса системы охлаждения, генератора, а на современных двигателях нередко и масляного насоса, ТНВД дизеля, и т. д.) благодаря его большой эластичности.
Недостатки — в большинстве выпускаемых двигателей обрыв ремня вызовет удар тарелок клапанов о поршни. Во избежание этого рекомендуется строго соблюдать установленную периодичность замены зубчатого ремня. Ресурс обычно составляет от 50 до 150 тыс. км. Но необходимо помнить, что резина стареет со временем, и при малых ежегодных пробегах замена ремня может потребоваться раньше, чем это установлено производителем. Необходимо также помнить, что к обрыву ремня может привести и неисправность роликов натяжения, поэтому если двигатель «втыковой» (то есть, обрыв или проскок ремня ГРМ приведёт к столкновению тарелок клапанов и поршней), то следует время от времени осматривать механизм зубчатого ремня. Заклинивание водяного насоса также обычно приводит к обрыву ремня со всеми его последствиями (типичная проблема двигателей ВАЗ с ременным приводом)[5].
В современных двигателях, у которых ремни выполнены из качественных синтетических материалов со стеклонитяными или проволочными кордами, обрыв приводного ремня в течение установленного для него срока его службы — редкое явление, обычно вызванное воздействием внешних факторов — к примеру, попадания на ремень масла, приводящего к его повреждению, попадания в привод посторонних предметов (наледи, частей разрушившихся деталей двигателя, ветоши при ремонте, и т. п.), неисправности или низкого качества изготовления натяжных роликов (перекос, заклинивание), заклинивания подшипников насоса системы охлаждения, и так далее. Также обрыв ремня ГРМ или срезание части его зубьев особенно часто происходит во время пуска двигателя зимой в морозную погоду (из-за увеличения усилия прокручивания распредвалов) или после длительного простоя автомобиля.
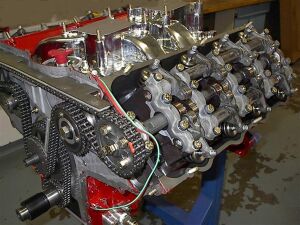
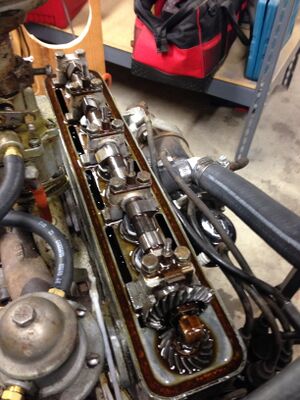
Цепной привод ГРМ является распространенным в верхнем ценовом сегменте легковых автомобилей, используется в двигателях внедорожников и грузовых автомобилей, требования к которым подразумевают повышенный уровень надёжности и живучести. Цепь обычно сдвоенная (двухрядная), реже — однорядная или многорядная, малошумная роликовая или втулочно-роликовая («цепь Галля») либо бесшумная пластинчато-зубчатая («цепь Морзе»), находится в объёме двигателя, омываемом маслом. На двигателях с двумя распределительными валами, а также V-образных, могут применяться приводы ГРМ с несколькими цепями. Для предотвращения колебаний цепи и её перескакивания между зубьями звёзд цепной привод ГРМ оснащается натяжителями и успокоителями цепи. Натяжители цепи выполняются либо в виде вращающегося ролика, либо в виде пластмассового «башмака». Регулирование усилия натяжения цепи может быть полуавтоматическим или автоматическим. В двигателях с полуавтоматическим регулированием регулировка осуществляется либо за счёт стопорного болта, либо цанговым зажимом («Жигули»). После правильной регулировки пружина натяжителя обеспечивает необходимое усилие натяжения цепи. На современных двигателях как правило применяется автоматическое регулирование натяжения цепи, осуществляемое гидронатяжителем. На ведущих участках цепи устанавливаются успокоители из антифрикционной пластмассы[5].
Преимущества цепного привода ГРМ: отсутствие опасности внезапного обрыва — изношенная цепь начинает стучать, особенно на холодном двигателе, предупреждая владельца о необходимости замены; больший ресурс — в 2-3 раза больше, чем у зубчатого ремня, и фактически сравнимый с ресурсом двигателя в целом. Недостатки — дороговизна, несколько больший уровень шумности и вибраций. Натяжитель цепи («башмак») изнашивается сильнее, чем натяжные ролики ремня, и требует периодической замены, а сама конструкция натяжного устройства цепи сложнее и должна выдерживать большие нагрузки. Сильно изношенная цепь может растягиваться (даже очень малый, на несколько микронов, износ отдельных звеньев в сумме приводит к значительному растяжению цепи в целом) и в какой-то момент перескакивать через один или несколько зубьев звёздочки — к катастрофическим для мотора последствиям это не приводит, но вызывает смещение фаз газораспределения и, соответственно, существенное нарушение его работы, которое не всегда сразу верно диагностируется при ремонте из-за сходства симптомов с иными неисправностями.
Стоит отметить, что в последнее время, в особенности на западноевропейских моторах, получил широкое распространение привод ГРМ «удешевлённой» однорядной пластинчато-зубчатой цепью. Такая цепь не имеет преимуществ перед ремнём с точки зрения ресурса, а по сравнению с классической двухрядной более склонна к растяжению и обрыву.
В некоторых двигателях использовался привод распределительного вала промежуточным валом с коническими шестернями на концах, примеры — двигатели американской фирмы Crosley[англ.], танковый дизель В-2 (последний имеет по два распределительных вала на головку и по четыре клапана на цилиндр).
Десмодромный газораспределительный механизм
В нём используются два распределительных вала (либо один, но с кулачками сложной формы): один перемещает клапаны вниз, второй — вверх. Клапанные пружины отсутствуют.
Двигатели с десмодромным газораспределением могут работать на оборотах, недоступных для обычных клапанных механизмов с пружинами, у которых при определённых оборотах коленчатого вала скорости срабатывания клапанных пружин не будет хватать для того, чтобы отвести клапаны из-под удара поршня до его прихода в верхнюю мёртвую точку («зависание» клапанов), что приводит к выходу двигателя из строя.
Десмодромный механизм имеет много прецизионных деталей, очень трудоёмок и дорог в изготовлении, требует высочайшего качества моторного масла. Этот механизм применялся на ряде гоночных автомобилей, например, Mercedes-Benz W196[16], O.S.C.A. Barchetta[англ.]* и Mercedes-Benz 300 SLR, а ныне — на мотоциклах Ducati[17][18].
В качестве альтернативы десмодромному механизму используется закрытие клапанов при помощи пневматических толкателей[19].
В двухтактных двигателях
В двухтактных дизельных двигателях большого объёма с клапанно-щелевой продувкой обычно имеются только выпускные клапана, устроенные в целом аналогично выпускным клапанам бензинового двигателя, а для впуска сжатого воздуха во время продувки используются впускные окна в стенках цилиндра, открываемые уходящим вниз поршнем. В большинстве случаев используется привод ГРМ типа OHV, ничем принципиально не отличающийся от такового на бензиновом моторе.
ГРМ с изменяемыми фазами газораспределения
Механизмы, позволяющие прямо во время работы двигателя изменять длительность и высоту открытия выпускных клапанов, использовались ещё в начале XX века — например, на авиационном моторе Gnome-Monosoupape первых лет выпуска (с 1913 года) при помощи такого механизма осуществлялось управление оборотами. Однако чисто-механические системы изменения фаз газораспределения широкого распространения не получили — недостаточно точное управление процессом приводило к тому, что в некоторых режимах работы происходил перегрев клапанов, приводящий к их прогоранию. Интерес к ним возник лишь после резкого ужесточения требований к экономичности и экологичности двигателей, а также развития управляющей микроэлектроники, позволившего полноценно реализовать эту идею.
В настоящее время большинство производителей автомобилей мирового уровня предлагают на некоторых своих двигателях систему изменения фаз газораспределения, которая регулирует параметры открытия клапанов в соответствии со скоростью вращения и нагрузкой на двигатель, благодаря чему достигается более эффективное использование мощности двигателя, снижается расход топлива, снижается загрязнённость выхлопа. В частности, существуют варианты такой системы разработки фирм Honda (VTEC), Toyota (VVT-i), Mitsubishi (MIVEC), Nissan (VVL), BMW (VANOS), Ford (Ti-VCT), Subaru (AVCS) и других.
ГРМ без распределительного вала
Вместо механического привода клапанов непосредственно от кулачков распределительного вала в этих конструкциях используются электрический (электромагниты или соленоиды), гидравлический или пневматический привод клапанов. Это сулит значительные выгоды благодаря возможности повышения коэффициента наполнения цилиндров, снижения потерь на газообмен за счёт использования цикла Миллера, применения адиабатного расширения заряда рабочей смеси, снижающего его температуру и, соответственно, выбросы оксида азота, а также предотвращения аномальных процессов горения (детонации и т. п.). Однако реализация данного принципа встречает на своём пути огромные затруднения[5].
Начиная с 1950-х годов во многих странах велись опытно конструкторские работы по оснащению клапанов поршневого двигателя внутреннего сгорания электромагнитным приводом, в частности — в СССР под руководством профессора МАДИ Владимира Митрофановича Архангельского. Однако у наиболее простого варианта электромагнитного привода клапана, в котором его открытие осуществлялось за счёт воздействия электромагнитного поля, а закрытие — обычной клапанной пружиной, был вскоре выявлен целый ряд критических недостатков. В частности, масса клапана вместе с плитой, обеспечивающей его притягивание к электромагниту, оказалась намного больше, чем в традиционном ГРМ, что обуславливало большую инертность механизма привода и вынуждало значительно увеличивать жёсткость клапанной пружины, а это приводило к сильному удару клапана о седло при закрывании и его быстрому выходу из строя. Кроме того, состояние электротехники в середине XX века ещё не позволяло создать электронный блок управления, позволяющий контролировать закрывание и открывание клапанов, а использовавшееся, в частности, в работах Архангельского электромеханическое управление ГРМ, с приводящимися от кулачков распределительного вала контактами и коммутационными реле, страдало целым рядом недостатков, в частности — постоянным подгоранием и выходом из строя контактов реле, коммутирующих необходимые для работы электромагнитов большие токи.
Поэтому исследователи переключились на вариант, в котором как открытие, так и закрытие клапана осуществлялось при помощи электромагнитов, без участия пружин. В частности, в 1970-х годах над подобной схемой работали в Тольяттинском государственном университете под руководством профессора В. В. Ивашина. Распределительный вал был полностью устранён из конструкции, а сила тока, необходимая для работы привода клапанов, уменьшилась по сравнению с конструкцией Архангельского на порядок.
В 1980-х годах в НАМИ под руководством кандидата технических наук А. Н. Терехина велась разработка варианта двигателя автомобиля «Москвич-412» с электромагнитным приводом клапанов, доведённая до стадии действующего макета ГРМ, в котором на всех восьми клапанах использовались двусторонние электромагниты. Прекращение финансирования в 1990-х годах привело к остановке работ.
В 2002 году фирма BMW приступила к натурным испытаниям 16-клапанного двигателя с электромагнитным приводом клапанов. Аналогичные работы ведутся и многими другими производителями.
Тем не менее, применительно к быстроходным автомобильным двигателям в настоящее время данная технология не вышла из стадии опытно-конструкторских работ. Фирмы MAN (серия ME) и Wartsila (серия RT-flex) выпускают серийно тихоходные стационарные и судовые дизельные двигатели без распределительного вала.
С гильзовым управлением газораспределением
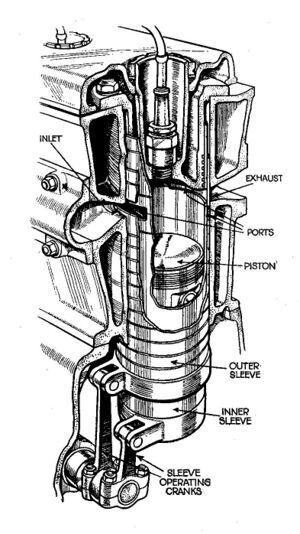
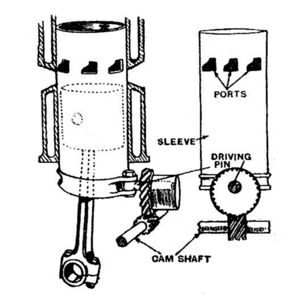
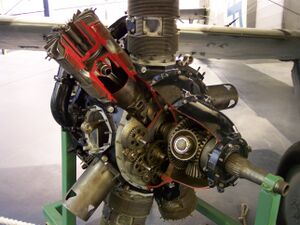
Эта конструкция впервые была разработана американским инженером Чарльзом Найтом (Charles Yale Knight), часто по его фамилии называется «системой Найта»[англ.], хотя Найт разработал лишь один из типов гильзового газораспределения — с двумя скользящими гильзами, расположенными одна внутри другой и движущимися в противоположных направлениях. В такой конструкции гильза цилиндра выполняется в виде подвижной вдоль оси цилиндра детали, имеющей привод от распределительного вала через пару косозубых шестерён. Этот привод обеспечивает перемещение гильзы вверх-вниз, синхронизированное с движением поршня. Окна в стенках гильзы при этом в определённый момент оказываются напротив ответных окон в стенке цилиндра, тогда через них осуществляется впуск рабочей смеси и выпуск отработанных газов.
Главное преимущество гильзового газораспределения — полная бесшумность работы двигателя, поскольку в его работе полностью отсутствуют удары деталей друг о друга. Кроме того, для неё характерны высокая долговечность, нетребовательность к обслуживанию и хорошее наполнение цилиндров бензовоздушной смесью за счёт большого размера и меньшего сопротивления окон в гильзах по сравнению с каналами клапанов — особенно относительно нижнеклапанных двигателей.
В то же время, двигатель с гильзовым газораспределением сложен по конструкции, нетехнологичен и дорог в изготовлении. Кроме того, неистребимым недостатком системы со скользящими гильзами являлся высокий расход масла на угар — обеспечить надёжное уплотнение пары трения «цилиндр — гильза» было практически невозможно, так что масло в значительных количествах прорывалось внутрь цилиндра, где сгорало вместе с рабочей смесью.
Применялась в основном на дорогих легковых автомобилях — в первую очередь нужно отметить целую серию моделей SS (San-Soupape, фр. «без клапанов») французской фирмы Panhard et Levassor и автомобили фирмы Avions Voisin с двигателями Найта, а также такие модели, как Willys-Knight и Mercedes-Knight. Полный список автомобилей с двигателями Найта включает такие марки и модели, как:
- Brewster;
- Columbia;
- Daimler;
- Falcon-Knight (1928—1929);
- Mercedes-Benz;
- Minerva;
- Moline-Knight (1914—1919);
- Panhard et Levassor;
- Peugeot and Mors;
- R&V Knight (1920—1924);
- Silent-Knight (1905—1907);
- Stoddard-Dayton;
- Stearns-Knight (1911—1929);
- Avions Voisin (1919—1938);
- Willys-Knight (1915—1933);
Также гильзовое газораспределение находило применение на авиадвигателях, в частности, на британских авиационных двигателях разработки тридцатых годов, таких, как Bristol Perseus, Bristol Hercules. Аналогичные конструкции широко применялись и на паровых двигателях.
На британских авиадвигателях применялась не система Найта, а система МакКаллума, в которой гильзы (одна на цилиндр) не скользили вдоль цилиндра, а вращались относительно него, что было проще в реализации. Также существовало небольшое число двигателей, имевших окна не сбоку цилиндра, а в самой головке блока, то есть более близких к традиционной системе с тарельчатыми клапанами.
Преимущества этой системы были особенно заметны по сравнению с нижнеклапанными автомобильными двигателями первой половины XX века, после появления гидрокомпенсаторов клапанного зазора и массового распространения верхнеклапанных ГРМ традиционного типа они практически исчезли. Тем не менее, впоследствии, вплоть до нашего времени, ряд исследователей высказывал мнение, что в двигателях будущего возможен возврат к системе Найта или иному виду гильзового газораспределения.
Примечания
- ↑ Орлин А.С. Двигатели внутреннего сгорания. Устройство и работа поршневых и комбинированных двигателей.. — 4-е. — Москва: Машиностроение, 1990. — С. 79—85. — 289 с.
- ↑ Дьяченко В. Газообмен в ДВС. — 1989.
- ↑ Что такое система изменения фаз газораспределения (рус.) (7 января 2016). Архивировано 18 октября 2018 года. Дата обращения 18 октября 2018.
- ↑ Экономичность - двигатель - Большая Энциклопедия Нефти и Газа, статья, страница 1 . www.ngpedia.ru. Дата обращения: 13 апреля 2019. Архивировано 13 апреля 2019 года.
- ↑ 5,00 5,01 5,02 5,03 5,04 5,05 5,06 5,07 5,08 5,09 5,10 5,11 Дмитриевский А. В. Автомобильные бензиновые двигатели. М.: Астрель, 2003.
- ↑ Б. Гусев, Л. Лепарский. Отличный мотор ждёт работы. «АэроМастер», № 1/98.
- ↑ 7,0 7,1 7,2 7,3 7,4 7,5 Отечественные автомобили (справочник). Ленинград, 1964 год.
- ↑ 8,0 8,1 8,2 8,3 8,4 8,5 8,6 8,7 8,8 8,9 Автомобильные двигатели. Под ред. М. С. Коваха. М., «Машиностроение», 1977.
- ↑ 9,0 9,1 А. А. Сабинин. Скоростные автомобили. М., «Физкультура и спорт», 1953 год.
- ↑ Army Service Corps Training, Mechanical Transport, 1911.
- ↑ А. М. Кригер. Автомобильный двигатель ЗИЛ-130. Возможности форсировки двигателя ЗИС-120 и преимущества V-образных двигателей.
- ↑ В. И. Анохин. Советские автомобили. Справочник. М., Государственное научно-техническое издательство машиностроительной литературы, 1955 год.
- ↑ David Greenlees. An early Cameron automomobile mystery. . theoldmotor.com. Дата обращения: 13 января 2019. Архивировано 24 декабря 2018 года.
- ↑ William Pearce. Lancia Tipo 4 and Tipo 5 V-12 Aircraft Engines. . oldmachinepress.com. Дата обращения: 13 января 2019. Архивировано 16 марта 2019 года. Old Machine Press, 2014 год (в статье также приведён список источников).
- ↑ Схематическое изображение . www.curbsideclassic.com. Дата обращения: 13 января 2019. Архивировано 10 октября 2015 года. двигателя Lycoming V12.
- ↑ Авторевю № 2, 2002. История с картинками. Mercedes 300 SLR (недоступная ссылка). www.autoreview.ru. Дата обращения: 26 июля 2010. Архивировано 26 июля 2010 года.
- ↑ Ducati. История марки . www.italynews.ru. Дата обращения: 13 января 2019. Архивировано 8 июля 2014 года.
- ↑ История клапанной системы Ducati Desmodromic / Ducati / bikepost.ru — блогосоциальный сервис для мотоциклистов . www.bikepost.ru. Дата обращения: 13 января 2019. Архивировано 13 марта 2016 года.
- ↑ Мэтт Соммерфилд. Второй пит-стоп Квята в Австралии. Зачем он был нужен? . ru.motorsport.com (27 марта 2017). Дата обращения: 8 апреля 2017. Архивировано 8 апреля 2017 года.
Литература
- Рикардо Г.Р. Быстроходные двигатели внутреннего сгорания. — М.: ГНТИ Машиностроительной литературы, 1960.
Для улучшения этой статьи желательно: |