Электрохимическая обработка
Стиль этой статьи неэнциклопедичен или нарушает нормы литературного русского языка. |
Электрохимическая обработка (ЭХО) — способ обработки электропроводящих материалов, заключающийся в изменении формы, размеров и (или) шероховатости поверхности заготовки вследствие анодного растворения её материала в электролите под действием электрического тока.
Виды электрохимической обработки
Возможно, эта статья содержит оригинальное исследование. |
Электрохимическое объемное копирование — Электрохимическая обработка, при которой форма электрода-инструмента отображается в заготовке
Электрохимическое прошивание — Электрохимическая обработка, при которой электрод-инструмент, углубляясь в заготовку, образует отверстие постоянного сечения
Струйное электрохимическое прошивание — Электрохимическое прошивание с использованием сформированной струи электролита
Электрохимическое калибрование — Электрохимическая обработка поверхности с целью повышения её точности
Электрохимическое точение — Электрохимическая обработка, при вращении заготовки и поступательном перемещении электрода-инструмента
Электрохимическая резка — Электрохимическая обработка, при которой заготовка разделывается на части
Электрохимическое удаление заусенцев (ЭХУЗ, Electrochemical debuting) — Электрохимическая обработка, при которой удаляются заусенцы заготовки
Электрохимическое маркирование
Многоэлектродная электрохимическая обработка — Электрохимическая обработка осуществляемая электродами, подключенными к общему источнику питания электрическим током и находящимися во время обработки под одним потенциалом
Непрерывная электрохимическая обработка — Электрохимическая обработка при непрерывной подаче напряжения на электроды
Импульсная электрохимическая обработка — Электрохимическая обработка при периодической подаче напряжения на электроды
Циклическая электрохимическая обработка — Электрохимическая обработка, при которой один из электродов перемещается в соответствии с заданной циклограммой,
а также другие смешанные виды электрофизикохимической обработки (ЭФХМО) включающие ЭХО:[источник не указан 2149 дней]
- анодно-механическая обработка;
- электрохимическая абразивная обработка;
- электрохимическое шлифование;
- электрохимическая доводка (ЭХД);
- электрохимическое абразивное полирование;
- электроэрозионнохимическая обработка (ЭЭХО);
- электрохимическая ультразвуковая обработка и др.
Физико-химическая сущность метода
Возможно, эта статья содержит оригинальное исследование. |
Механизм съёма (растворения, удаления металла) при электрохимической обработке основан на процессе электролиза. Съём металла происходит по закону Фарадея, согласно которому количество снятого металла пропорционально силе тока и времени обработки. Один из электродов (заготовка) присоединен к положительному полюсу источника питания и является анодом, а второй (инструмент) — к отрицательному; последний является катодом.
Особенностями электролиза являются пространственное окисление (растворение) анода и восстановление (осаждение) металла на поверхности катода. При ЭХО применяют такие электролиты, катионы которых не осаждаются при электролизе на поверхности катода. Этим обеспечивается основное достоинство ЭХО перед электроэрозионной обработкой — неизменность формы электрода-инструмента. Для стабилизации электродных процессов при ЭХО и удаления из межэлектродного промежутка продуктов растворения (шлама) применяют принудительную подачу в рабочую зону электролита, то есть прокачивают его с определенным давлением.
История развития электрохимической обработки (ЭХО)
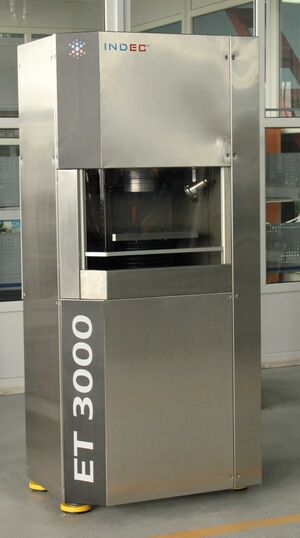
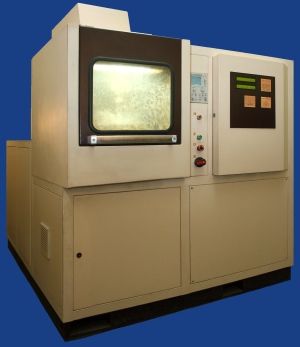
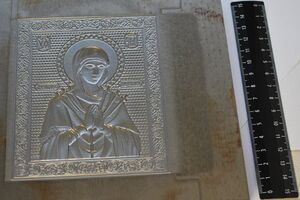
- 1911 г. Приоритет открытия методов электрохимической обработки металлов принадлежит русским учёным. Своё начало электрохимическая обработка берёт от процесса электрохимического полирования, предложенного ещё в 1911 г. известным русским химиком Е. И. Шпитальским.
- 1928 г. Первые опыты В. Н. Гусева по интенсификации обработки деталей машин привели к тому, что ещё в 1928 г. удалось осуществить электрохимическую обработку станин крупных металлорежущих станков. Тогда-то и было предложено В. Н. Гусевым (в соавторстве с Л. А. Рожковым) вести процесс ЭХО на узких МежЭлектродныхПромежутках (до десятых долей миллиметра) с принудительной прокачкой электролита (А. С. № 28384 от 21.03.28г.).
- 1941-1945 гг. В. Н. Гусеву, его сотрудникам Е. А. Дрозду, И. Я. Богораду и другим удалось разработать анодно-механический метод обработки.
- 1947-1950 гг. В эти годы определились три разновидности обработки металлов, использующей электрохимические явления: размерная электрохимическая, анодно-механическая и анодно-абразивная. В 1948 г. в лаборатории В. Н. Гусева была создана электрохимическая установка для обработки в потоке электролита, которая впервые была применена для изготовления отверстий в броневой стали. Тогда же были проведены первые опыты по обработке турбинных лопаток. Через несколько лет в нашей стране впервые в мировой практике было осуществлено промышленное внедрение операций электрохимического формообразования.
- 1962 г. Создание технологического процесса снятия заусенцев разработанного в ЭНИМСе В. Ю. Вероманом, И. А. Байсуповым и др.
- 1963 г. А. Н. Голдобиным, Ю. И. Коптеевым и др. было предложено сложно-контурное вырезание электродом- проволокой.
- 60-е гг. В СССР была создана гамма электрохимических станков для снятия заусенцев, плоскошлифовальных, для двусторонней обработки и копировально-прошивочных, работающих на постоянном токе. (Каталог-справочник. Электрофизические и электрохимические станки. М. 1969 г.)
- 65-68 гг. В 1965 г. начал выходить журнал «Электронная обработка материалов», а с 1968 г. «Электрофизические и электрохимические методы обработки».
- 70-80-е гг. Появилась возможность перейти на импульсные и импульсно-циклические методы обработки. В эти годы в Советском Союзе работали научные центры по развитию ЭХО на базе академической науки, отраслевых НИИ, высших учебных заведений, крупных промышленных предприятий в городах: Москве, Кишинёве, Туле, Ленинграде, Иваново, Казани, Куйбышеве, Ереване, Уфе, Новосибирске и т. д. Регулярно проводились Отраслевые, Всесоюзные и Международные конференции по электрофизическим и электрохимическим методам обработки. В Советском союзе были созданы и внедрены в производство электрохимические копировально-прошивочные станки: 4412, 4412ФЦ, 4420, 4420Ф4, 4420ФЦ, 4420Ф11, 4А420/Ф11, 4А420/Ф3, 4а420/Ф3М, 4421, 4421ФЦ, 4422, 4423, 4423ФЦ, МА4423, 4А423ФЦ, 4424, МА4424, АГЭ-10, АГЭ-11, АТ-80, АТ-90, СЭП902, СЭП902М, СЭП902МА, СЭП902П, СЭП902А, СЭХО-4А, СЭХО-41, Э-402, Э-460, Э-468, ЭГС-2, ЭГС-29, ЭКУ-150, ЭКУ-151, ЭКУ-152, ЭКУ-400, ЭКУ-1503, ЭРО-120, ЭХС-12М и др. В 1986 году в СССР вышел новый каталог-справочник «Электрофизические и электрохимические станки» В Советском Союзе были проведены глубокие исследования теории процесса ЭХО (Ф. В. Седыкин, Ю. Н. Петров, В. Д. Кащеев и др.) Значительные успехи в разработке теоретических основ и совершенствовании технологии получены также В. П. Смоленцевым, И. И. Морозом, Д. З. Митяшкиным, Д. Т. Васильевым, Л. Б. Дмитриевым, Г. Н. Знигерманом, В. В. Бородиным, Г. Н. Зайдманом, В. А. Шманёвым, Ю. В. Головачёвым, В. Г. Филимошиным, А. К. Журавским, Д. Я. Длугачем, Г. А. Алексеевым, В. В. Любимовым, В. Ф. Орловым, Б. И. Чугуновым, Б. Н. Кабановым, Я. М. Колотыркиным, А. Г. Атанасянцем, А. И. Дикусаром, Г. С. Доменте, Г. Р. Энгельгардтом и др. В этот период разработкой электрохимических станков занимались во многих странах мира: США (Chem-Form Ex-Cell-0, Cincinnati Milling Co, Anocut Eng), Великобритании (Mechem), Франции (Qualitex), Чехословакии (Vuma), Нидерландах (Philips), Японии (Mitsubishi Electric Co, Hitachi Ltd), Швейцарии (Chamilles), ФРГ (R. Bosch, AEG-ELOTHERM).
- 1986 г. В городе Туле прошла последняя в Советском Союзе VI Всесоюзная научно-техническая конференция «Электрохимическая размерная обработка деталей машин». При этом на внешне благополучном фоне «громом среди ясного неба» прозвучала информация во вступительном слове председателя Я. М. Колотыркина о том, что на Западе сворачиваются все разработки, связанные с электрохимической размерной обработкой, и усилия направляются на эрозионную обработку, так как на Западе увлеклись обработкой на постоянном токе, а электрохимическое оборудование оставалось громоздким, энергоёмким и зачастую уже не соответствовало возросшим требованиям по точности формообразования.
- 1988 г. Создание и внедрение в производство электрохимического станка ЭС-4000 с площадью обработки до 40 см², конкурентоспособного по точности обработки по отношению к электроэрозионным станкам.
- 90-е гг. Сотни станков ЭС-4000 внедрены в производство в России и за рубежом. Работа на Международных выставках серии ЕМО (Милан, Ганновер, Париж) показала отсутствие на рынке подобного оборудования.
- 1998 г. Разработка нового электрохимического станка ЭС-80 с площадью обработки до 80 см².
- В 80-е — 90-е годы развитие получили более совершенные схемы импульсной и импульсно-циклической обработки в пассивирующих кислородосодержащих электролитах (водные растворы NaNO3, KNO3, NaClO3, Na2SO4, и т. п.), позволившие снизить погрешность обработки до 0,02…0,05 мм и шероховатость до Ra 0,2…0,4 мкм.
В начале XXI века наблюдается возросший интерес к электрохимическому формообразованию. Появляются фирмы, как в России, так и за рубежом по разработке нового оборудования. В связи с появлением высокотехнологичных отраслях промышленности (точного приборостроения, медицины и медицинской техники, авиадвигателестроения и др.) новых групп высокопрочных и твёрдых материалов (в том числе наноструктурированных), усложнением формы деталей и ужесточением требований к качеству поверхностного слоя, возникла потребность в новых технологиях электрофизической и электрохимической обработки. Реакцией на этот запрос технического прогресса явилось появление в 1998—2011 годах целого комплекса новых способов биполярной микросекундной ЭХО вибрирующим электродом, предложенных авторским коллективом ООО «ЕСМ» (г. Уфа, Россия). Особенностью этих способов состоит в том, что они осуществляются на сверхмалых (3…10 мкм) межэлектродных зазорах с использованием групп импульсов тока высокой плотности (порядка 10²…104 А/см²). При их реализации становится достижимым обеспечение малых погрешностей (0,001..0,005 мм) обработки, создание на поверхностях деталей регулярных макро- и микрорельефов с в микронном и субмикронном диапазоне, и получение оптически гладких поверхностей (Ra 0,1..0,01 мкм). И все это при существенно более высокой (в сравнении с конкурирующим технологиями) производительностью на финишных операциях.
1989-2003 гг. производство серийных станков ЭС-4000, ЭС-80.
2003 г. Запущены в серийное производство электрохимические прошивные станки SFE-4000M и SFE-8000M
- 2008—2012 Гамма прецизионных электрохимических копировально — прошивочных станков: ЕТ500, ЕТ1000, ЕТ3000, ЕТ6000-3D (трёхкоординатный станок)
- 2010: системы ЕТ-ЕСО экологической чистоты электрохимической технологии для всех типов электрохимических станков
- 2011—2012 специальные электрохимические станки sET8000-2D и sET6000-3D для обработки лопаток авиационных двигателей и блисков
- 2014 г. Серийное производство электрохимических копировально-прошивных станков SFE-5000M
- 2017 г. Серийное производство электрохимических копировально-прошивных станков SFE-12000M с площадью обработки до 120 кв.см.[источник не указан 2149 дней]
Электрохимический станок
Возможно, эта статья содержит оригинальное исследование. |
Технологические установки для реализации процесса ЭХО как правило являются узкоспециализированными под определенный технологический процесс, в связи с низкой производительностью (в сравнении с другими методами формообразования: механическая обработка, электроэрозионная обработка) и сложностью процесса. Однако ЭХО обладает рядом уникальных технологических свойств (постоянство формы обрабатывающего электрода, обработка твёрдых и хрупких токопроводящих сплавов, обработка которых механическими методами резания и шлифования невозможна, или низко производительна, минимальные нагрузки на обрабатываемую заготовку позволяют обрабатывать тонкостенные, ажурные детали, отсутствие измененного слоя в детали после обработки (оплавление, наклёп, термоупрочнение) поверхностного слоя, возможность подвода исполнительного органа (электрода) в труднодоступные полости и отверстия деталей) которые позволяют осуществлять обработку деталей, неосуществимую другими известными методами обработки.
Широкое распространение электрохимические станки получили в авиационной промышленности. Распространены установки для получения рабочей поверхности пера лопатки турбореактивных двигателей (лопаточные станки), данные станки позволяют получать готовые изделия с минимальным применением доводочных, слесарных операций, требующих больших затрат времени и высококвалифицированного персонала. Именно по этим причинам большинство специализированных электрохимических установок уникально и изготавливается в единичном числе.
Однако, распространены и универсальные электрохимические станки, выпускаемые серийно, как правило, это копировально-прошивочные станки, позволяющие обрабатывать широкую номенклатуру деталей прямым копированием. Данные станки обладают одной координатой Z (которая осуществляет формообразование) иногда снабжаются дополнительными координатами (X и Y) для настройки и базирования взаимного расположения электрода и обрабатываемой поверхности в заготовке. Данные станки широко применяются в инструментальной промышленности для обработки штампов, пуансонов и других твёрдосплавных формообразующих технологических элементов.[источник не указан 2149 дней]
Литература
- Справочник по электрохимическим и электрофизическим методам обработки//Г. Л. Амитан, И. А. Байсупов, Ю. М. Барон и др.; Под общ. ред. В. А. Волосатова.-Л.: Машиностроение. Л, 1988.-719с.: ил. ISBN 5-217-00267-0
- Житников В. П., Зайцев А. Н. Импульсная электрохимическая размерная обработка.-М.: Машиностроение, 2008- 413с.ISBN 978-5-217-03423-9
- ГОСТ 25330-82 Обработка электрохимическая. Термины и определения
- Электрохимическая обработка металлов / А. Д. Давыдов // Большая российская энциклопедия : [в 35 т.] / гл. ред. Ю. С. Осипов. — М. : Большая российская энциклопедия, 2004—2017.
Ссылки
- [bse.sci-lib.com/article126201.html Электрофизические и электрохимические методы обработки] — статья из Большой советской энциклопедии
Примечания